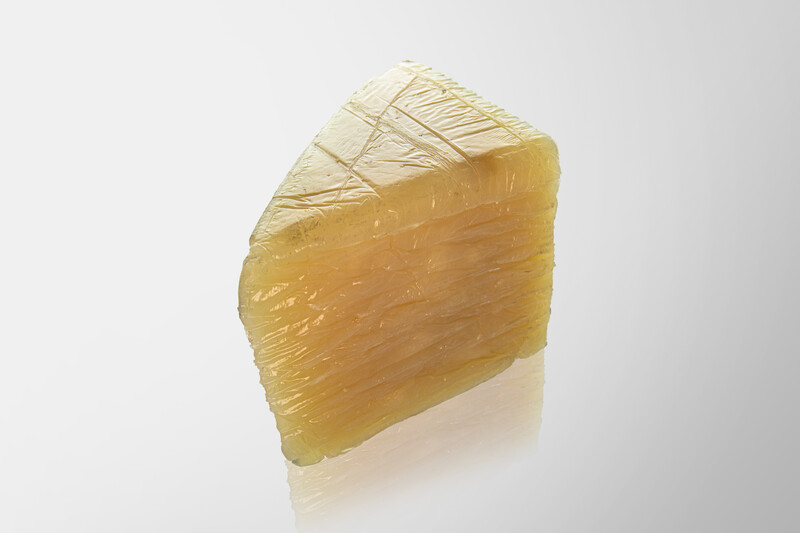
JÄGER Business Blog
WHITEPAPER
Erfahren Sie, welche Faktoren Ihren SOP beeinflussen!
Dichtungen sind dafür da, unerwünschte Stoffübergänge innerhalb von technischen Produkten zu verhindern. Weil es sich um verhältnismäßig preisgünstige Komponenten handelt, genießen sie in der Konstruktion zumeist keine hohe Priorität. Daher provozieren Dichtungen in Entwicklungs-Projekten häufig Probleme, denn jeder Anwendungsfall bringt eigene Anforderungen an ein Dichtungselement mit sich, die Konstrukteur:innen zwingend bekannt sein müssen.
In diesem Beitrag werfen wir einen Blick auf drei typische Probleme, die durch einen nachlässigen Umgang mit Dichtungen in der Entwicklung von Maschinen und Geräten entstehen können. Dazu verraten wir Ihnen, wie Sie die beschriebenen Schwierigkeiten wirksam vermeiden können.
Ob (und wie lange) eine Dichtung die ihr zugewiesene Aufgabe erfüllen kann, hängt nicht zuletzt von ihrer Einbauumgebung ab. Selbst für einfache O‑Ringe müssen in der Konstruktion z. B. geeignete Nuten oder Vertiefungen eingeplant werden, in welche die Dichtung eingefasst werden kann. Komplexer gestalten sich die Voraussetzungen für ausgefeilte Elemente wie Rotations- oder Hydraulikdichtungen, deren Anforderungen in der Konstruktion spezifisches Know-how erfordern.
Wenn der vorgesehene Bauraum für eine Dichtung ungenügend ist, kann das Probleme verursachen. Typisch ist, dass bestehende Konstruktionszeichnungen zu einem späten Zeitpunkt im Produktentstehungsprozess (PEP) angepasst werden müssen, was zusätzliche Entwicklungsschleifen erfordert. Um dies zu verhindern, entscheiden sich manche Unternehmen für hochkomplexe Dichtungselemente, die für das Projekt erst noch konzipiert werden müssen – inklusive kostspieliger Werkzeugkonzepte. Im schlimmsten Fall wird eine Dichtung mangelhaft verbaut, sodass sie im Einsatz früher oder später versagt. Bei einem Hersteller von Elektronikgeräten führte eine unsauber verbaute Dichtung beispielsweise dazu, dass die Elektronik mit Staub in Berührung kam und nach kurzer Zeit komplett ausfiel.
Produzierende Unternehmen, die Verzögerungen, Folgekosten und Reputationsverluste vermeiden wollen, müssen die Anforderungen jeder Dichtungskomponente (Bauraum, funktionale Anforderungen etc.) bereits in ihren Konstruktionszeichnungen ausreichend berücksichtigen. Das bedeutet jedoch nicht, dass Konstrukteur:innen ihre Maschinen um die Dichtung herum konzipieren sollten. Ein einfacher Maßnahmenkatalog, in dem alle relevanten Anforderungen und Prozesse aufgeführt sind, kann die beschriebenen Schwierigkeiten oft im Keim ersticken.
Auch für Dichtungen gelten teilweise strenge gesetzliche Vorgaben und Qualitätsstandards. Entsprechende Anforderungen müssen Konstruktions-Teams bereits zu Beginn des Entwicklungs-Projekts kennen, um eine Dichtung richtig auslegen zu können. Andernfalls kommt es auch hier zu teuren Verzögerungen und zusätzlichen Entwicklungsschleifen.
Ein Beispiel hierfür ist die Brandklassifikation UL94. Diese kommt zum Einsatz, wenn ein Kunststoffartikel einem gewissen Brandrisiko ausgesetzt ist und daher flammresistent sein muss. In manchen Fällen vergessen Unternehmen, dass diese Eigenschaft das gesamte Produkt betreffen muss, nicht nur einzelne Komponenten. Sie verwenden für das Gehäuse zwar einen UL94-klassifizierten Kunststoff, aber nicht für die Dichtung. Infolgedessen ist das Gesamtprodukt nicht ausreichend flammresistent, was weitere Zertifizierungen beeinträchtigen kann.
Solche Probleme sind bei der Entwicklung von Dichtungskomponenten nicht ungewöhnlich. Sie lassen sich mit einer gewissenhaften Materialauswahl umgehen. Dabei müssen Unternehmen im Vorfeld alle relevanten Rahmenbedingungen analysieren, die für die Dichtung von Bedeutung sind. Neben rechtlichen Vorgaben zählen dazu:
Entscheidend sind bei der Materialauswahl Sorgfalt, Erfahrung und Fachwissen. Per se gibt es für jede Dichtung ein geeignetes Material. Die Herausforderung ist, aus der Vielzahl an Werkstoffen die Mischung zu identifizieren, mit der sich die Anforderungen an die Dichtung am besten umsetzen lassen.
In der Regel fokussieren sich Konstruktions-Teams zunächst auf Metallkomponenten. Gummi- und Kunststoffteile erhalten erst dann ihre Aufmerksamkeit, wenn das Produkt zum großen Teil fertig designt ist. Das heißt jedoch, dass die Anforderungen der Dichtungstechnik über einen großen Teil des Konstruktionsprozesses kaum Beachtung finden. Für Lieferanten von Gummi- und Kunststoffkomponenten stellt dies eine Herausforderung dar, denn sie sollen Dichtungen liefern, die sich in der vorgesehenen Form entweder gar nicht oder nur mit hohem finanziellem Aufwand herstellen lassen. Beide Szenarien wirken sich negativ auf Termin- und Kostenvorgaben im PEP aus.
Schwierigkeiten verursacht vor allem die geometrische Ausgestaltung des Bauteils, in dem die Dichtung verbaut werden soll. Spitze Ecken und Kanten, komplizierte Winkel sowie ausgefallene Formen lassen sich, wenn überhaupt, nur mit hohem Aufwand abdichten. Das gleiche gilt für Bauteile, in denen Höhenunterschiede bestehen. Diese erschweren es, eine Dichtung gleichmäßig anzubringen, da die Materialmischung in der Fertigung nicht gleichmäßig verpresst werden kann. Folglich müssen Dichtungshersteller auf komplexe, aufwendige Fertigungsverfahren zurückgreifen, um die Anforderungen ihrer Kunden zu erfüllen.
Werden Dichtungen in der Konstruktion zu spät berücksichtigt, verhindert dies häufig den Einsatz kostengünstiger, fertigungstechnisch einfacher zu realisierender Lösungen. Standarddichtungen (z. B. O‑Ringe), die ohne dediziertes Werkzeugkonzept einfach hinzugekauft werden könnten, lassen sich beispielsweise in komplexen Geometrien nicht einsetzen. Einsparpotentiale – nicht nur monetär, sondern auch hinsichtlich des CO2-Fußabdrucks des Unternehmens (Materialausschuss, Energieeinsatz etc.) – bleiben auf diese Weise ungenutzt.
Wesentlich sinnvoller ist es, wenn Konstrukteur:innen bereits bei der Planung die Voraussetzungen berücksichtigen, die für eine Dichtung gegeben sein müssen. Ihr erster Ansatz sollte darin bestehen, möglichst häufig auf Standardkomponenten zurückzugreifen. Ist dies ausgeschlossen, sollten Konstruktions-Teams am besten früh den Kontakt zu Materialexpert:innen suchen. Deren Know-how erleichtert es, mit Blick auf monetäre Vorgaben und fertigungstechnische Umsetzungsmöglichkeiten die beste Lösung zu entwickeln.
Bereits kleine Nachlässigkeiten können in der Dichtungstechnik Schadensfälle, aufwändige Entwicklungsschleifen und zusätzliche Kosten nach sich ziehen. Umso wichtiger ist es, dass Konstruktions-Teams sich bereits zu Beginn des Projektes ausführlich mit den Rahmenbedingungen befassen, denen ihre Dichtungen ausgesetzt sind. Das betrifft u. a. den notwendigen Bauraum, das zu verwendende Material sowie die Geometrie der Komponenten, in denen die Dichtungen eingebaut werden sollen.
Whitepaper: Den Start of Production sichern
Tim Eltze ist seit mehr als 20 Jahren im Bereich der Gummi- und Kunststoffprodukte tätig und verfügt über ein fundiertes Fachwissen in diesen Bereichen. Aktuell ist er bei Jäger als Regionalleiter Nord und Standortleiter Hamburg beschäftigt.
Jetzt Beitrag teilen!
Jäger Gummi und Kunststoff GmbH
Lohweg 1
30559 Hannover
Tel. +49 511 – 53580
Fax +49 511 – 553394
info@jaeger-gk.de
Geschäftsführung:
Dipl.-Ing Sebastian Jäger
Julius Jäger, M.Sc.
Registergericht Hannover HRB 59798
DE 813 314 161