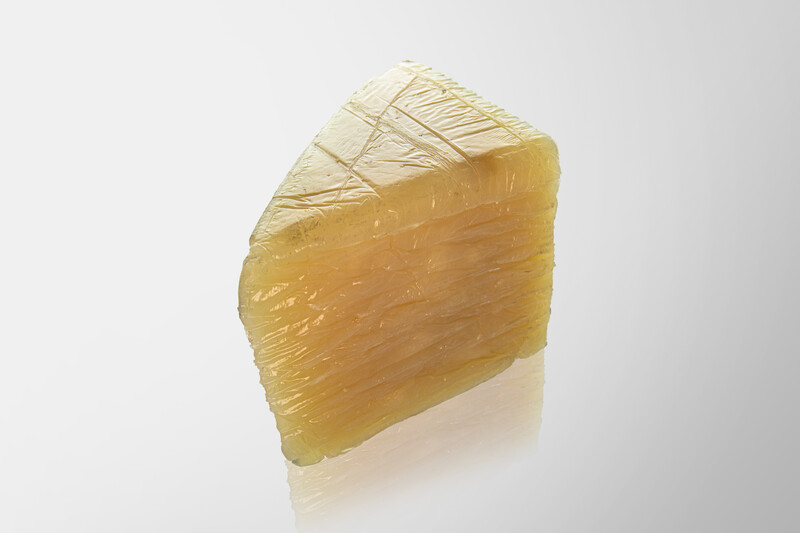
Fachbeitrag
WHITEPAPER
Erfahren Sie, welche Faktoren Ihren SOP beeinflussen!
In der Konstruktion ergeben sich Optimierungspotenziale hauptsächlich durch eine flexible, fertigungsgerechte Gestaltung der Komponenten sowie des Produkts selbst. Eine Herausforderung ist hier, dass Konstrukteur:innen oft aus dem Metallbereich stammen und ihren Fokus entsprechend ausrichten. Da sie nur begrenztes Wissen über Elastomere und Kunststoffe verfügen, konzentrieren sie sich darauf, die Metallkonstruktion zu optimieren, ihre Kernkompetenz. Diesen Umstand zu überwinden ist die erste Herausforderung bei der Optimierung von Gummi- und Kunststoffkomponenten in der Konstruktion.
Großes Optimierungspotenzial besteht bei der Materialauswahl und damit verbunden auch beim Produktdesign. Oft ergibt es Sinn, das verwendete Material eines Formteils auf den Prüfstand zu stellen und kritisch zu begutachten, ob nicht ein alternativer Werkstoff die Anforderungen besser erfüllt. Zum einen entwickelt sich die Materialwirtschaft ständig weiter, zum anderen treffen Unternehmen bei der Neuentwicklung einer Komponente manchmal Entscheidungen, die sich im Nachhinein als falsch erweisen. In beiden Fällen lohnt es sich, die Materialauswahl zu hinterfragen und gegebenenfalls den Werkstoff zu wechseln.
Oftmals ergibt es auch Sinn, parallel den Aufbau einer Komponente zu überdenken. Materialauswahl und Produktdesign gehen Hand in Hand. In manchen Szenarien ist es zum Beispiel möglich, das Gewicht einer Komponente durch eine Designänderung zu reduzieren, die weniger Material vorsieht, aber gleichzeitig einen robusteren Kunststoff verwendet. Auch die Materialkosten, die Lebensdauer des Formteils oder seine CO2-Bilanz können durch solche Änderungen deutlich verbessert werden.
Vor einiger Zeit kam ein Kunde mit dem Auftrag auf uns zu, die Druckrollen seiner Förderbänder zu optimieren. Diese waren relativ energie- bzw. kostenintensiv in der Herstellung. Unsere Fachexpert:innen ersetzten das Teil durch einen Kern aus leichterem Polypropylen, der von einer vulkanisierten Gummi-Komponente ummantelt ist. Dadurch sanken sowohl die Herstellungskosten als auch der Material- sowie der Energieaufwand. Die Details können Sie in unserer Case Study nachlesen.
Fließfehler zu verhindern ist einerseits Erfahrungssache. Erfahrene Konstrukteur:innen entwickeln mit der Zeit ein Gespür für das Fließverhalten einer Gummi- bzw. Kunststoffmischung und können es zumindest bei einfachen Geometrien gut abschätzen. Bei komplexeren Formen empfiehlt es sich, das Fließverhalten des Werkstoffs mit Hilfe der Finite-Elemente-Methode (FEM) und spezieller Software zu simulieren. Im Zweifelsfall ergibt es auch hier Sinn, Fachexpert:innen hinzuzuziehen.
Unternehmen, die mehrere Produkte oder Produktlinien fertigen, sollten in Erwägung ziehen, ihre Gummi- und Kunststoffkomponenten zu standardisieren. Auf diese Weise können sie ihr gesamtes Sortiment mit den gleichen Formteilen versorgen, statt immer wieder neue Entwicklungsprojekte zu starten. Diese Plattformbauweise ist in der Automobilbranche gang und gäbe, aber auch andere Branchen können davon profitieren.
Die modulare Gestaltung von Gummi- und Kunststoffformteilen senkt zum einen die Entwicklungskosten, da die Konstruktion leichter auf Standardkomponenten zurückgreifen und der Einkauf Skaleneffekte durch die Bestellung größere Mengen einheitlicher Artikel realisieren kann. Zum anderen sinken die Entwicklungszeiten, da die Konstruktion entsprechender Gummi- oder Kunststoffteile entfällt.
Um die hier beschriebenen Potenziale auszuschöpfen, braucht es Materialkompetenz im Bereich Gummi und Kunststoff. Unternehmen, denen dieses Wissen fehlt, sollten daher möglichst früh mit einem spezialisierten Entwicklungspartner zusammenarbeiten und dessen Expert:innen von Beginn an in das Entwicklungs-Team einbinden. Das erleichtert es, Bauteile gleich richtig auszulegen. Je früher dieser Partner alle relevanten Informationen in Form eines Lastenheftes erhält, desto effizienter gestaltet sich erfahrungsgemäß das Entwicklungsvorhaben.
Der zweite große Optimierungsblock betrifft die Produktionsprozesse, sprich: alles was nach dem Einkauf des Rohmaterials und vor dem Versand aus dem Logistikzentrum geschieht. Hier geht es vor allem darum, Durchlaufzeiten, Standzeiten, die Ausschussquote und den Ressourceneinsatz zu reduzieren. Die wichtigsten Stellhebel sind die Produktionsplanung und das Werkzeugdesign.
Im Gegensatz zu den anderen Optimierungsbereichen ist die Prozesstechnik fast ausschließlich in der Domäne des Gummi- oder Kunststofflieferanten angesiedelt. Kunden haben relativ wenig Einfluss auf die eigentliche Fertigung von Formteilen. Wollen sie dennoch Optimierungspotenziale in diesem Bereich realisieren, müssen sie darauf achten, Zulieferer zu wählen, die entsprechende Kompetenzen vorweisen.
Voraussetzung für alle Optimierungsmaßnahmen in der Prozesstechnik ist eine gründliche Analyse der zu fertigenden Artikel sowie der Rahmenbedingungen hinsichtlich der Fertigung auf Kundenseite. Dazu gehören unter anderem folgende Fragen:
Große Verbesserungsmöglichkeiten ergeben sich bei der Erstellung der Werkzeugkonzepte. Ganz gleich ob Gummi oder Kunststoff: Spritzgussformen sind Präzisionswerkzeuge, deren Geometrie exakt mit den Vorgaben der Konstruktion übereinstimmen muss. Schon kleinste Abweichungen von diesen Vorgaben können dazu führen, dass die Funktionalität des Bauteils gefährdet ist. Dementsprechend braucht es ausführliche Vorbereitung und Erfahrung, um Fehler, die den termingerechten Projektabschluss in Gefahr bringen, wirksam auszuschließen.
Der Werkzeugbau ist in der Elastomer- und Kunststoffproduktion eine projektinterne Großbaustelle, die alle in der Produktion gängigen Prozessschritte beinhaltet und u. a. Konzepte für Konstruktion, Fertigung sowie Transport erfordert. Dieser komplexe Prozess lässt sich nicht einfach verkürzen oder beschleunigen. Stattdessen sollten Unternehmen für den Bau der Werkzeuge ausreichend Zeit einplanen.
Die Firma Protecfire, ein Brandschutzspezialist aus Lübeck, wandte sich an Jäger mit einer Anfrage für eine Löschanlage, die Motorbrände in Bussen bekämpfen soll. Gefordert war eine Gummiblase, die im Notfall Löschflüssigkeit in die Leitungen presst. Jäger entwickelte für den Kunden eine entsprechende Elastomer-Komponente und erstellte ein Werkzeugkonzept, das eine zuverlässige Kernzentrierung und damit eine hohe Qualität garantiert. Weitere Details zu diesem Projekt finden Sie in unserer Case Study.
Die Fertigungszeit von Spritzgussformteilen hängt unter anderem davon ab, wie schnell sich die Rohmasse innerhalb des Werkzeugs verteilt. Die Verteilungsgeschwindigkeit wiederum richtet sich nach dem Aufbau des Werkzeugs, insbesondere nach der Anzahl der Kavitäten. Je mehr Kavitäten vorliegen, desto mehr Rohmasse kann gleichzeitig in die Formen gespritzt werden und desto weniger Material muss über Kanäle verteilt werden. Gleichzeitig sinken die angussbedingten Materialverluste, da weniger Gummi bzw. Kunststoff in den Kanälen zurückbleibt.
Allerdings steigt mit der Anzahl der Kavitäten auch die Größe des Werkzeugs, was dessen Kosten erhöht. Zugleich muss das Werkzeug auch in die Spritzgießmaschine passen und kann nicht beliebig groß sein. Beide Faktoren müssen sorgfältig bedacht werden. Ein größeres Werkzeug zu bauen ist nicht immer die beste Lösung.
Material, das nach der Fertigstellung der Formteile in den Kanälen des Werkzeugs zurückbleibt, muss entweder wiederverwertet oder entsorgt werden. Dies erhöht die Stückkosten, insbesondere bei der Herstellung von Gummikomponenten, da der Vulkanisierungsprozess irreversibel ist. Aus diesem Grund ist die Reduzierung von Angussverlusten ein wichtiger Optimierungsansatz in der Prozesstechnik.
Insbesondere die Heiß- und Kaltkanaltechnik sind an dieser Stelle zu erwähnen. Beide temperieren das Angusssystem separat und verhindern somit, dass der Werkstoff vorzeitig erhärtet. Im Fall der Kunststoffverarbeitung werden die Kanäle beheizt, damit die Mischung erst in den Formen erstarrt. Bei Elastomerprodukten werden die Kanäle dagegen gekühlt.
Standzeiten sind in der Produktion immer ein Problem, denn wenn eine Maschine oder Anlage nicht läuft, erwirtschaftet sie auch keinen Ertrag. Daher gilt es auch im Gummi- und Kunststoffbereich, die Standzeiten zu optimieren.
Die primären Stellhebel hierfür sind im Spritzgussverfahren die Temperatur, der Einspritzdruck sowie die Kühl- bzw. Heizdauer des Werkzeugs, was wiederum die Zykluszeiten beeinflusst. Hinzu kommen noch die Auswahl des passenden Materials sowie intelligentes Werkzeugdesign. Der fehlende Einfluss des Kunden macht sich in diesen Bereichen besonders bemerkbar. Daher sollten Unternehmen bei der Lieferantensuche darauf achten, Produktionspartner zu wählen, die entsprechende Kompetenzen aufweisen.
Die Herausforderung bei der Materialauswahl besteht darin, eine Werkstoffmischung zu finden, die sich am besten für den geplanten Einsatzzweck des Produktes eignet. Dies wirkt sich nicht nur positiv auf die Qualität des zu entwickelnden Produktes aus. Intelligente Entscheidungen bei der Materialauswahl können dazu beitragen, die Gesamtkosten für das Produkt zu reduzieren (z. B. durch einen verringerten Materialeinsatz) und den CO2-Footprint des Unternehmens zu verbessern (z. B. durch die Reduzierung von prozessbedingtem Abfall). Falsche Entscheidungen verschlechtern hingegen die Funktionalität und Zuverlässigkeit des Bauteils – und damit auch der Maschine oder Anlage.
Wesentliche Erfolgsfaktoren bei der Auswahl des passenden Materials sind Fachkompetenz und Erfahrung. Die besten Ergebnisse erzielen Unternehmen, wenn sie Materialexpert:innen von Beginn an in ihr Entwicklungs-Team integrieren. Dies ermöglicht nicht nur eine schnelle, gezielte Auswahl der richtigen Kunststoff- oder Gummimischung, sondern auch eine enge Verzahnung aus Mischungsentwicklung, Mischungsfertigung sowie der Analyse der physikalischen Eigenschaften. Die Zahl der Entwicklungszyklen lässt sich dadurch auf das Nötigste beschränken.
Unternehmen, die für ihre Gummi- und Kunststoffkomponenten speziell angefertigte Materialmischungen verwenden, leiden oft unter hohen Einkaufspreisen. Der Grund dafür ist, dass die Knetmaschinen der Werkstofflieferanten für den Betrieb eine Mindestmenge an Rohstoffen benötigen. Dies ist in der Regel auch die vertragliche Mindestabnahmemenge für den Kunden. Bei Sondermischungen ist es schlichtweg nicht möglich, bedarfsgerecht einzukaufen. Wenn der Anbieter beispielsweise fünf Tonnen produziert, muss der Kunde auch fünf Tonnen abnehmen, auch wenn er nur eine Tonne benötigt. Die restlichen vier Tonnen würde der Anbieter sonst nicht loswerden, denn sie sind individuell an die spezifischen Vorgaben eines Unternehmens angepasst.
Anders sieht die Sache aus, wenn Unternehmen Standardmischungen ordern. Für diese finden sich so viele Abnehmer, dass einzelne Kunden auch geringere Mengen bestellen können als das Fassungsvermögen eines Bottichs. Somit ist eine bedarfsgerechte Bestellung möglich.
Bei der Materialauswahl sind oft zwei Extreme zu beobachten. Einige Unternehmen stellen den Preis in den Vordergrund und wählen einen möglichst günstigen Werkstoff. Andere entscheiden sich für die Premiumvariante und verwenden ein Material, das ihre Anforderungen weit übertrifft. Beides kann negative Folgen haben.
Den Preis zu minimieren führt häufig dazu, dass die Gummi- oder Kunststoffkomponente eine niedrige Qualität hat und häufig ausgetauscht werden muss. Daraus entstehen Folgekosten, welche den geringen Einkaufspreis schnell relativieren und zu unerwünschten Verzögerungen führen. Dazu besteht die Gefahr, dass sich Billigteile aus Prozess- und Materialsicht negativ auf die Klimabilanz des Unternehmens auswirken.
Das andere Extrem, die unnötige Auswahl von Premiummaterialien, erhöht die Produktionskosten, ohne einen reellen Gegenwert zu bieten. Teils spielen die gestiegenen Eigenschaften für das Endprodukt nicht einmal eine Rolle. „Viel hilft viel“ ist im Gummi- und Kunststoffbereich nicht immer die richtige Lösung.
Besser ist, das Material präzise auf die Anforderungen des Einsatzszenarios zuzuschneiden. Ausreißer in Richtung Preis oder praktischer Charakteristika sind selten hilfreich.
Lieferschwierigkeiten im Materialbereich wirken sich oft auf die gesamte Wertschöpfungskette aus, da das Fehlen einzelner Komponenten die Fertigung weiterer Produkte beeinträchtigt. Unternehmen, deren Gummi- und Kunststoffkomponenten regelmäßig nicht lieferbar sind, sollten daher einen Materialwechsel in Erwägung ziehen. Oft gibt es alternative Werkstoffe, die vergleichbare Eigenschaften haben und deutlich leichter zu beschaffen sind.
Darüber hinaus lohnt es sich, die Rohstoffmärkte im Auge zu behalten. Lieferschwierigkeiten bestimmter Materialien sind oft das Resultat vorhersehbarer Entwicklungen. Wer diese erkennt, kann frühzeitig Gegenmaßnahmen ergreifen. Im Zweifelsfall ist es sinnvoll, diesbezüglich den Austausch mit Gummi- oder Kunststoffproduzenten zu suchen, die den Markt genauer kennen.
Bei der Entwicklung eines neuen Formteils gehört die Auswahl des Materials zu den grundlegenden Schritten. Insbesondere wenn es sich um Mischungen handelt, die speziell für ein Produkt bzw. Bauteil entwickelt werden, müssen Unternehmen hierfür eine entsprechende Vorlaufzeit kalkulieren, denn die Mischung muss im Labor hinsichtlich ihrer Eigenschaften ausführlich erprobt werden. Dieser Prozess nimmt Zeit in Anspruch, die rechtzeitig eingeplant werden muss, um Verzögerungen im Produktentstehungsprozess zu vermeiden.
Aus diesen Gründen birgt die Umstellung der Lieferketten auf europäische Lieferanten großes Optimierungspotenzial – aktuell mehr denn je.
Redundanz ist ein wichtiger Optimierungsfaktor im Supply Chain Management. Wer all seine Gummi- und Kunststoffkomponenten von einem Zulieferer bezieht, schafft sich einen künstlichen Flaschenhals, dessen Ausfall gravierende Konsequenzen haben kann. Daher empfiehlt sich der Aufbau eines strategischen Lieferantennetzwerks, um im Bedarfsfall schnell auf einen anderen Anbieter wechseln zu können. Zu Bedenken ist auch, dass einige Gummi- und Kunststoffproduzenten ihre eigenen Lieferantennetzwerke haben und daher eine gewisse Grundredundanz aufweisen. Es ist also nicht unbedingt nötig, dass der Kunde alle Zulieferer selbst koordiniert. Zudem lassen sich in diesem Fall die Bedingungen der Partnerschaft in Rahmenverträgen festlegen, um zusätzliche Sicherheit zu gewährleisten.
Industrieunternehmen tragen bei der Umsetzung nationaler und globaler Nachhaltigkeitsziele eine große Verantwortung. Daraus ergeben sich zahlreiche Pflichten, aber auch Chancen, die eigene Organisation besser für die Zukunft aufzustellen. Das wird am Beispiel von Bauteilen aus Gummi und Kunststoff immer wieder deutlich. Deren Fertigung ist grundsätzlich energieintensiv – allerdings bestehen je nach Szenario Möglichkeiten, den Energieverbrauch und Schadstoffausstoß bei der Gestaltung von Produkten und Prozessen auf das Nötigste zu reduzieren. Entscheidend ist in diesem Zusammenhang ein sinnvoller Dreiklang aus
Etwa 96 Prozent der Zulieferer von Jäger Gummi und Kunststoff haben ihren Sitz innerhalb der Europäischen Union, 80 Prozent von ihnen in Deutschland. Diese Lieferanten werden gezielt aufgrund ihrer Zertifizierung nach der Umweltnorm DIN EN ISO 14001 sowie (idealerweise) der DIN EN 50001 ausgewählt. Unternehmen, die ihre Beschaffung nachhaltig gestalten wollen, stehen hierfür also ideale Bedingungen offen.
Whitepaper: Den Start of Production sichern
Jetzt Beitrag teilen!
Weitere Beiträge
Jäger Gummi und Kunststoff GmbH
Lohweg 1
30559 Hannover
Tel. +49 511 – 53580
Fax +49 511 – 553394
info@jaeger-gk.de
Geschäftsführung:
Dipl.-Ing Sebastian Jäger
Julius Jäger, M.Sc.
Registergericht Hannover HRB 59798
DE 813 314 161