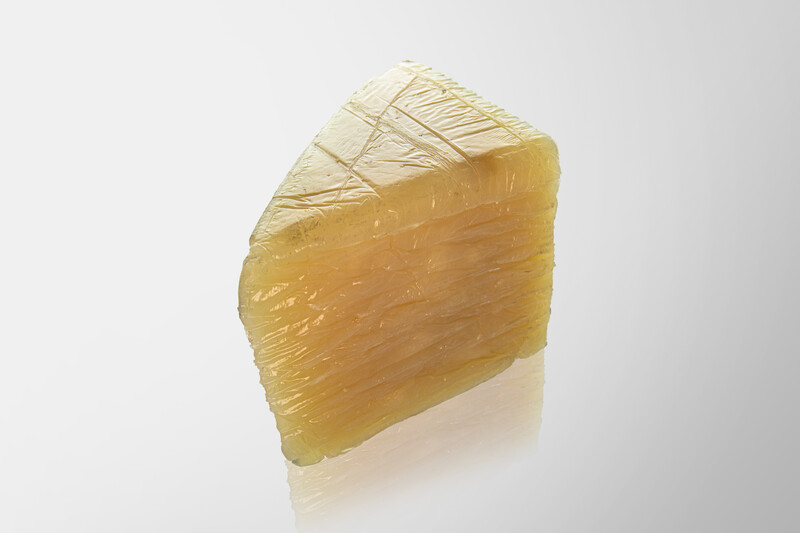
JÄGER Business Blog
WHITEPAPER
Erfahren Sie, welche Faktoren Ihren SOP beeinflussen!
Voraussetzung für eine erfolgreiche Nachhaltigkeitsstrategie ist eine ausführliche Wissensbasis. Daher haben wir zunächst untersucht, welche Unternehmensbereiche wie viel Energie verbrauchen. Im Zuge dessen konnten wir sechs große Energieverbrauchsgruppen identifizieren:
Diese Analyse bildete die Grundlage, um unsere energetische Ausgangsbasis zu bestimmen – eine Gegenüberstellung des Inputs, aufgespalten in Energieträger, und des Outputs, also des Energiekonsums pro Verbrauchsstelle. Die primären Energieträger bzw. -arten der Firma Jäger sind Erdgas, Heizöl und Strom. Dem gegenüber stehen folgende Verbrauchsstellen bei Artemis:
Anhand unserer Analyse konnten wir den Energieverbrauch sowie den CO2-Ausstoß pro verarbeitetem Kilogramm Gummimasse berechnen. Das Ergebnis haben wir als Ist-Zustand angenommen sowie als Kennzahl, um die Effektivität unserer Verbesserungsmaßnahmen zu bewerten.
Auf Basis der Verbrauchsanalysen haben wir eine Reihe von Optimierungsmaßnahmen identifiziert und umgesetzt. Einige davon waren technischer Natur, andere betrafen eher organisationale Faktoren.
Unsere erste Optimierungsmaßnahme bestand darin, den Energieträger zu wechseln. In der Vergangenheit gewann Jäger Wärmeenergie hauptsächlich aus Erdöl. Mittlerweile sind wir größtenteils auf Erdgas umgestiegen, welches einen deutlich geringeren CO2-Ausstoß aufweist.
Angesichts der geopolitischen Lage ist diese Maßnahme nicht in Stein gemeißelt. Da wir die Möglichkeit haben, sowohl Gas als auch Erdöl zu verwenden, ist auch ein hybrider Energiemix denkbar.
Parallel haben wir unsere Beleuchtung saniert. Statt HQL-Leuchten verwenden wir nun ausschließlich LED-Lampen. Diese sind zum Teil mit einer Tageslichtsensorik ausgestattet, die den Energieverbrauch auf das Notwendigste reduziert. Dadurch konnten wir den Energieaufwand für die Beleuchtung um 70 Prozent reduzieren.
Als Nächstes befassten wir uns mit dem Thema Formisolierung und Wärmedämmung. Zu diesem Zweck statteten wir den Großteil unserer Injection-Molding-Formen mit Isolierschichten aus und verbesserten die maschinenseitige Isolierung, damit die Formen keine Wärme mehr an den Maschinenrahmen abgeben. In Kombination haben diese Maßnahmen den Energieaufwand pro Quadratmeter Form um 1,4 kW reduziert.
Isolierte Werkzeugform in der Produktion
Auch die Antriebs- und Steuerungstechnik war Gegenstand unserer Optimierungsmaßnahmen. So verwenden unsere Spritzgussanlagen nun keine konventionellen Hydraulikmotoren und -pumpen mehr, sondern eine Kombination kleinerer Servomotoren, die im Sinne einer bedarfsgerechten Servohydraulik alle einzeln angesprochen werden können.
Wo es ging, haben wir Frequenzumrichter nachgerüstet und energieeffizientere Antriebe eingesetzt. Neue Motoren dürfen einer internen Richtlinie zufolge nicht schlechter als IE3 sein.
Unsere Bestandsanlagen haben wir mit Phasenanschnittreglern ausgestattet, die bei Niedriglast- oder Leerlaufphasen die Leistung der Maschine kurzfristig drosseln und dadurch den Energieverbrauch senken. Dies ist besonders bei langen Heizphasen relevant und führte zu einer Energieeinsparung von ca. 10 Prozent.
Ein großes Thema war und ist die systematische Schwachstellenüberprüfung. Wir haben alle unsere Maschinen und Anlagen darauf untersucht, ob irgendwo Energie verloren geht. Dies umfasste unter anderem mögliche Druckluftleckagen, Schwachstellen in Dämmungsbereichen sowie eine Überprüfung von Dampfarmaturen mittels Schallmessung. Die identifizierten Leckagen oder Beschädigungen wurden anschließend von unserer Instandhaltung beseitigt. Hierbei handelt es sich um einen kontinuierlichen Prozess, den wir stets weiterführen.
Prüfung auf Leckage in der Produktion
Auf organisationaler Ebene haben wir vor allem ein abteilungsübergreifendes Bewusstsein für energieeffizientes Arbeiten geschaffen. So haben wir nun ein interdisziplinäres Energieteam, dem Vertreter:innen aller energierelevanten Bereiche sowie der Geschäftsführung angehören. Dieses Team kommt regelmäßig zusammen und bespricht Optimierungspotenziale sowie mögliche Verbesserungsmaßnahmen. Zudem haben wir ein betriebliches Vorschlagswesen etabliert, das es Mitarbeiter:innen ermöglicht, Ideen zum Energiesparen einzureichen.
Mithilfe der beschriebenen Maßnahmen ist es uns gelungen, zwischen 2012 und 2020 mehr als 2.000 Tonnen CO2 einzusparen. Zudem konnten wir in der gleichen Zeit den Energieverbrauch pro hergestelltem Kilogramm Gummi um 20 Prozent reduzieren.
Dadurch leisten wir nicht nur unseren Beitrag zur Bekämpfung des Klimawandels, sondern reduzieren obendrein unsere Energiekosten – ein Vorteil, den wir auch an unsere Kunden weitergeben. Beispielsweise sind wir weniger stark von Preisschwankungen auf den Energiemärkten betroffen und müssen daher steigende Kosten auch nicht vollständig an unsere Kunden weitergeben.
Whitepaper: Den Start of Production sichern
Jetzt Beitrag teilen!
Jäger Gummi und Kunststoff GmbH
Lohweg 1
30559 Hannover
Tel. +49 511 – 53580
Fax +49 511 – 553394
info@jaeger-gk.de
Geschäftsführung:
Dipl.-Ing Sebastian Jäger
Julius Jäger, M.Sc.
Registergericht Hannover HRB 59798
DE 813 314 161