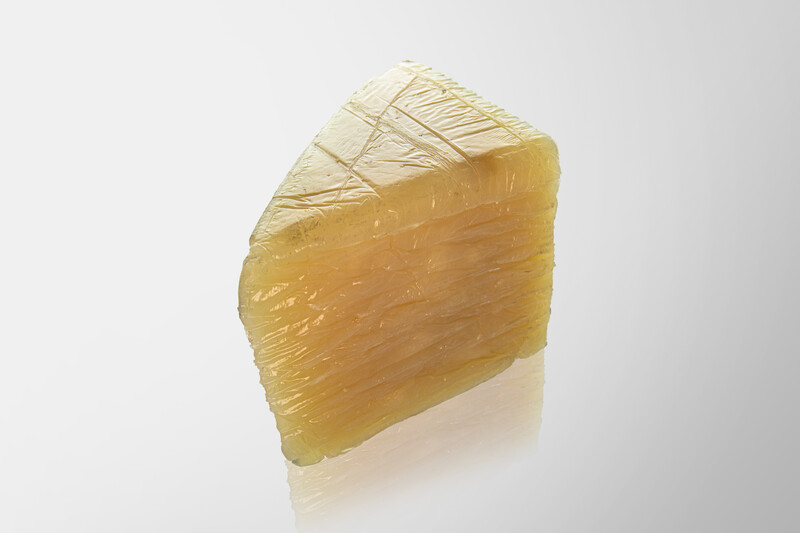
JÄGER Business Blog
WHITEPAPER
Find out which factors influence your SOP!
Before cooperation begins, the customer and supplier must ensure that they interpret the project requirements in the same way. Otherwise, the vendor may design a solution that does not meet the customer’s quality or functional requirements. The coordination meeting is designed to avoid this hassle.
As a rule, the coordination meeting takes place shortly after the order is received. An earlier point in time is also possible, e.g. shortly after the customer has contacted the supplier for the first time. In this case, the coordination meeting is part of the sales consultation.
The focus of the discussion depends on the task. If the customer already has detailed design drawings, the coordination meeting is more of an examination of feasibility by the supplier, supplemented by any suggestions for optimization.
If, on the other hand, the customer approaches a producer with a set of requirements, the coordination meeting takes on the character of a consultation. The supplier assesses the requirements, asks questions and proposes a suitable solution to the customer.
In both cases, the focus is on developing a common objective. The customer and supplier agree on what the component to be produced should look like and what properties it must have. The purpose of this is to avoid misunderstandings and unnecessary correction loops. These can be caused by simple communication errors (customer thinks A, supplier understands B) or by incorrect assumptions that are not clarified (customer thinks A is self-evident and does not need to be listed separately in the specifications).
The second variant in particular occurs relatively frequently in the rubber and plastics sector. Many companies transfer their experience with metals to other materials, although this does not correspond to reality. For example, strict tolerances are no problem in the metal sector, but are hardly feasible with rubber.
The coordination meeting fulfills an important task, as misunderstandings can be easily corrected at this early stage of the production process. At a later stage, adjustments involve considerably more effort and also costs, for example if the mold has to be adjusted after the initial sample.
Despite intensive coordination, misunderstandings are possible in development projects, for example when both sides interpret what is said differently. It is therefore necessary to create initial samples, which the customer and supplier can use to compare their understanding of the specifications under production conditions. This is done in the context of initial sampling as well as the initial sample report.
Initial samples are parts, products and materials that are manufactured completely with series-production equipment under series-production conditions and tested including all required or agreed properties and specifications. The basis includes approved drawings or CAD data sets as well as the required material.
What the sampling process looks like in concrete terms depends on the customer’s wishes and requirements. In any case, it includes a sample of the ordered parts in all agreed variants (depending on the customer’s requirements, also several samples) as well as the following documents:
Control of product samples in the production
Apart from its primary task of ensuring the quality of purchased parts, products and materials, the ISR serves three functions:
1. It provides assurance for the supplier. In the initial sample report, the supplier provides evidence that he has correctly interpreted the customer’s specifications and is capable of producing the part in the desired quality. After the initial sample approval, he is no longer exposed to the risk of having to bear the costs of subsequent product adaptation.
2. He protects the customer. With the initial sample, the customer receives a quality template whose reproducibility he can always refer to after approval. If the serial products deviate significantly from the initial sample, the customer has the option of requesting rectification.
3. He avoids misunderstandings. The initial sample demonstrates the supplier’s understanding of the requirements. It forms a basis for discussion, on the basis of which misinterpretations can be identified and eliminated. Once the initial sample report has been approved, none of the parties involved can claim that the other side has incorrectly described or understood the requirements.
In production, quality management covers not only the operational level, but also the communication between customer and supplier. Both sides must ensure that no misunderstandings occur during the coordination process, which otherwise result in delays and increasing costs.
The coordination meeting and the initial sample report are important building blocks in this process. Both serve to bring all parties involved to the table and clarify open points, whether in the conceptual context or under production conditions. This exchange of information is essential to ensure that the product is ready for series production. Therefore, manufacturing companies should pay the necessary attention to both the initial consultation and the sampling.
Whitepaper: Secure the Start of Production
Learn which factors influence your SOP!
Henning Kracht is a trained mechanical engineer and head of quality management at Jäger Gummi und Kunststoff.
Share this post!
Jäger Gummi und Kunststoff GmbH
Lohweg 1
30559 Hannover
Tel. +49 511 – 53580
Fax +49 511 – 553394
info@jaeger-gk.de
Management:
Dipl.-Ing Sebastian Jäger
Julius Jäger, M.Sc.
Hanover Register Court HRB 59798
DE 813 314 161
Petra Dirlenbach