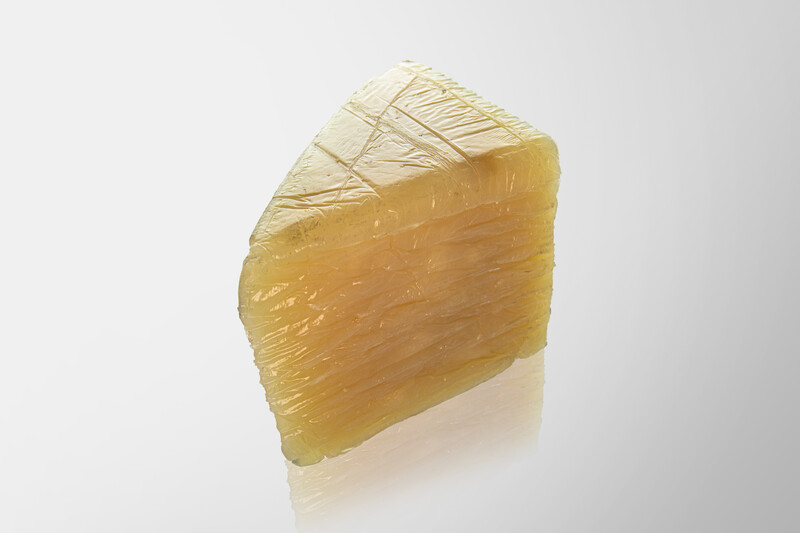
JÄGER Business Blog
WHITEPAPER
Find out which factors influence your SOP!
Silicone is frequently used as a material, especially in the pharmaceutical and food industries. However, it must not get into the human body, otherwise there is a risk of injuries or symptoms of poisoning. Accordingly, it is essential in these industries to be able to reliably detect and remove foreign bodies in products (for example, with the aid of a metal detector). The key word in this context is detectability.
Technology solutions are usually used for this purpose, because a purely visual inspection is not sufficient to detect all contaminants. This requires sensitive sensors as well as detectable materials that can be detected by machines in food and drugs.
Silicone is not inherently detectable. Neither is it magnetic, nor does its density differ significantly from other materials, making detection by X-ray scanner difficult. Therefore, it is usually necessary to change the material composition of the compound to make it detectable.
An object is detectable if it can be reliably detected in a medium surrounding it. In practice, different types of detectability exist, depending on the sensor technology used, e.g. X-ray or metal detectability.
There are several approaches to making a component detectable. In the context of silicone, the most common method is to add magnetic metal particles to the material, to which metal detectors respond.
For larger foreign bodies, infrared-based sensor detection is also possible. This responds to differences in surface texture. However, the technology is more likely to be used in product sorting, rather than in the context of safety and hygiene in the food industry.
Bellows made of silicone with detectable material
Additives that add detectable characteristics to a material simultaneously affect its material properties. This fact is not relevant in all areas. However, the design department should keep it in mind.
If silicone contains a detectable proportion of metal particles, it can no longer be processed in liquid form. The filler changes the flow properties too much. Production must instead work with solid silicone, which may require a different type of mold.
Another example concerns Shore hardness. Depending on the material, added fillers can increase or decrease the Shore value. Accordingly, the design department must counteract this to maintain the desired hardness of the silicone, for example by using a softer base material. Otherwise, the article may no longer meet the requirements defined at the beginning.
Changes to the material properties through the addition of fillers are particularly relevant if a silicone component is to be subsequently made detectable. The modifications may require an adaptation of the manufacturing process, especially of the mold. This may entail additional investment costs. Therefore, designers should consider in advance whether a component should be detectable and include this information in their specifications.
Detectable products are only one component in a safety concept that covers the entire production process. Companies must not only prevent foreign bodies from getting into their products, but also protect themselves in case this does happen. Detectability is a fallback in case of an emergency, but it should always be combined with robust hygiene and production concepts as well as forward-looking material selection.
Silicone products are detectable if additives are added to the material to change its characteristics and make it detectable to a metal detector, for example. This can be done with manageable effort, even away from food production.
The challenge is to maintain the desired material properties and quality despite the addition of additives. In most cases, it is necessary to adapt the formulation for this purpose. Therefore, companies should always note machine detectability in their specifications, if necessary. In this way, they can avoid expensive subsequent adjustments to their products.
Whitepaper: Secure the Start of Production
Learn which factors influence your SOP!
Tim Panster joined Jäger in 2019 as a sales representative for the Essen location. In 2020, he completed his Master of Science in Industrial Engineering at the FOM University of Economics & Management.
Share post now!
Jäger Gummi und Kunststoff GmbH
Lohweg 1
30559 Hannover
Tel. +49 511 – 53580
Fax +49 511 – 553394
info@jaeger-gk.de
Management:
Dipl.-Ing Sebastian Jäger
Julius Jäger, M.Sc.
Hanover Register Court HRB 59798
DE 813 314 161
Petra Dirlenbach