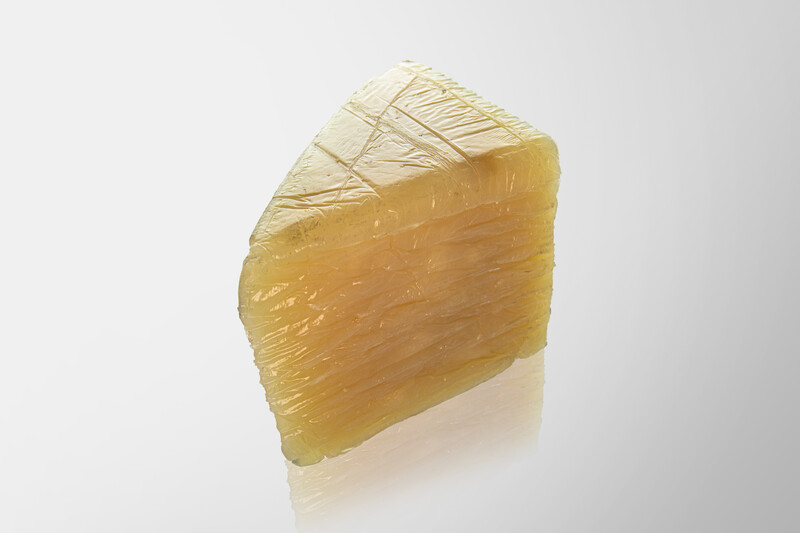
JÄGER Business Blog
WHITEPAPER
Find out which factors influence your SOP!
Fire protection is an important issue and, depending on the area of application, must be taken into account in the development of plastic and rubber components. If, for example, an electronic product or the equipment of a vehicle catches fire, not only material assets but also human lives are at risk. For this reason, the materials used must meet fire safety standards to provide the best possible protection in the event of a fire.
At Jäger, we encounter two of these standards particularly frequently: the American UL94 and the European DIN EN 45545.
UL94 is a fire protection standard issued by the U.S. organization Underwriters Laboratories (UL), which specializes in product and material certifications. The standard tests the flammability of plastics used in components in electrical and household appliances and has been harmonized with several international standards.
Its measurement criteria assess burning rate, extinguishing time, afterglow duration and droplet formation, among other things. In total, it includes twelve classifications, depending on the application of the material being tested:
The test method depends on the respective flammability class. The test specimen is aligned either horizontally (marking H) or vertically (marking V) and then exposed to a defined flame of a Bunsen burner for a certain time. The most stringent flame retardant classification is the 5VA test.
Test specimen in the flame of a bunsen burner
The horizontal HB classification tests the rate of fire after a single flame exposure, taking into account the thickness of the material. The vertical flammability classifications V-2 to V-0 flame test twice. They test burning and afterglow duration and test whether burning particles detach from the material sample, igniting a cotton indicator located under the test specimen.
Classes 5VB and 5VA have more stringent criteria. Here, the test specimen is exposed five times to a flame that is approximately ten times stronger than in the tests according to V-0, V-1, V-2 and HB. Both the burning behavior of vertically aligned bars and the hole formation on horizontally clamped plates are tested.
The VTM criteria are similar to those for classes V-2 through V-0, but the flame is applied for only 3 seconds instead of 10. For HBF tests, the flame application time is significantly longer at 60 seconds.
You can read the exact test criteria for the individual flammability classes on the Underwriters Laboratories website.
The standard is intended to ensure that passengers and train crews suffer as little damage to their health as possible in the event of a fire and can be evacuated smoothly. Material assets (e.g. the vehicle itself) play a subordinate role.
The design of the fire protection regulations in DIN EN 45545-2 depends on the hazard level. This is made up of the design class and the operating class, which are described in DIN EN 45545-1.
The design class categorizes the construction of the vehicle as well as its primary function:
The operating class reflects the conditions of use of the vehicle and thus the context of its operation:
The hazard level is derived from a matrix whose dimensions represent construction type and operating class. There are three categories: HL1 (low hazard), HL2 (medium hazard) and HL3 (high hazard).
N | A | D | S | |
OC1 | HL1 | HL1 | HL1 | HL1 |
OC2 | HL2 | HL2 | HL2 | HL2 |
OC3 | HL2 | HL2 | HL2 | HL3 |
OC4 | HL3 | HL3 | HL3 | HL3 |
The classification shows that the requirements increase the more critical the evacuation situation.
The test procedures and limit values provided for individual components depend on the hazard level and are described in detail in DIN EN 45545-2. The requirements differ, among other things, with regard to smoke development, oxygen content and the generation of toxic gases.
If you are interested, you can purchase the complete standard here.
The presumption is that the material with the highest fire protection class is always the best choice. However, maximizing the fire rating may mean that the material loses other desirable properties. Material selection in rubber and plastics is complex. There are several factors to consider in relation. Turning one screw can have consequences elsewhere.
For example, the use of additives that improve flame retardancy can have a negative impact on other properties, such as UV stability, flexural strength or temperature stability of the material. In addition, increased requirements for materials are often also associated with increased material costs and the choice of materials is narrowed down.
It therefore makes sense to coordinate the actual minimum requirements based on the application situation along the supply chain. Thus, in case of doubt, the use of an overqualified material, and thus higher material costs, can be avoided and a possible competitive disadvantage can be ruled out.
Whitepaper: Secure the Start of Production
Learn which factors influence your SOP!
Stefanie Schelberg is a trained industrial clerk and business administrator. She has been working in sales at Jäger since 2016 and is responsible for customer-specific products.
Share post now!
Jäger Gummi und Kunststoff GmbH
Lohweg 1
30559 Hannover
Tel. +49 511 – 53580
Fax +49 511 – 553394
info@jaeger-gk.de
Management:
Dipl.-Ing Sebastian Jäger
Julius Jäger, M.Sc.
Hanover Register Court HRB 59798
DE 813 314 161
Petra Dirlenbach