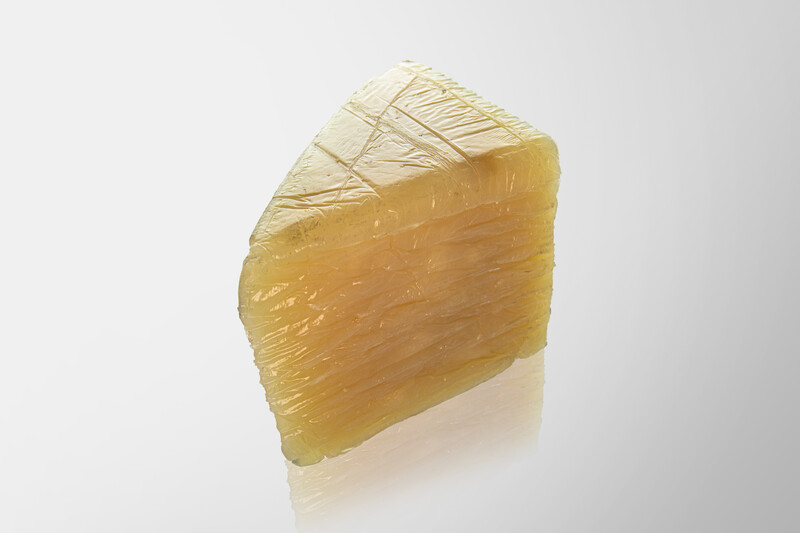
JÄGER Business Blog
you should consider
WHITEPAPER
Find out which factors influence your SOP!
Rubber-to-metal buffers are among the most common applications for elastomers. They are used whenever machinery or equipment needs to be protected from vibrations and shocks. Although they seem simple, their design is complex because there are a lot of influencing factors to consider.
Here are five facts about rubber-to-metal elements that companies should keep in mind.
Rubber and metal do not easily form a permanent bond. While it is possible to create a direct bond through process control and compatibility of the two components, this requires considerable effort and know-how. Companies typically use an adhesion promoter that serves as a chemical bridge and improves the adhesion properties of both elements. Strictly speaking, rubber-metal elements therefore consist not of two but of three elements: Elastomer, metal and adhesion promoter.
It is important that the adhesion promoter also receives attention during production. If it is damaged or compromised, there is a risk that the bond between the rubber and metal will be impaired.
For example, the adhesion promoter can be damaged if it is exposed to high temperatures for too long. However, injection molds are pre-tempered to speed up the vulcanization process. Therefore, it is important to reduce the exposure and molding times of rubber-to-metal elements. In this way, you avoid damage to the adhesion promoter.
Rubber-metal elements consist of different groups of materials that are chemically bonded together. Unlike composite materials, however, the materials retain their individual characteristics after vulcanization. This fact should also be taken into account in design and material selection. All components must meet the project requirements, otherwise the combined element is not suitable for the intended application.
For example, both the elastomer and the metal must have the right (shore) hardness or grade to meet the expected load. The same applies to resistances. If the element is intended for outdoor use, for example, all components must be optimized for outdoor use to the extent possible. The metal, for example, should have a corrosion coating suitable for the intended use, and the elastomer should have appropriate properties in its compound composition.
If rubber-metal elements are to carry large loads, for example, in addition to the component geometry, the weight distribution / center of gravity of the system is also of great importance. This is the case, for example, with machine feet. In addition to the component geometry and hardness, which are decisive for the stiffness of the bearing, the installation situation of the bearings and the geometry of the machine also play an important role in terms of static load and dynamic performance. If the center of gravity is exactly in the middle, all pedestals are equally loaded. However, if the machine is designed asymmetrically, the load is distributed unevenly. As a result, individual machine feet are exposed to higher static and dynamic loads than others. If this circumstance is not taken into account in the design and layout of the bearings, these components can fail in use after a short period of operation, which can cause further damage to the machine.
Therefore, certain input variables should be considered when designing rubber-to-metal elements.
The static load distribution, as well as further parameters (e.g. frequencies, amplitudes, etc.), are important input variables, because the overall performance depends on them, provided that the component is designed correctly.
Calculation of the static load distribution of a machine
Rubber-metal elements are mainly used to reduce shocks and vibrations. It is important to distinguish between damping and decoupling:
This distinction is important because it directly affects material selection. Each elastomer has different chemical and physical properties and responds differently to energy input. The storage modulus (G`) describes the energy that is stored after a force is applied to the bearing and can be recovered after the load is removed from the bearing. The loss modulus (G“), on the other hand, describes the viscous fraction of a material and thus the loss fraction of energy that is converted into heat by internal friction.
Natural rubber has a high storage modulus and a low loss modulus, i.e. it exhibits little energetic dissipation. Consequently, natural rubber is hardly suitable as a material for damping elements, because it converts only little kinetic energy into thermal energy. On the other hand, it has excellent decoupling properties. With butyl, the reverse is true. Put simply, it has a high loss modulus and a low storage modulus, so it is very well suited for damping components.
When selecting the base polymer, in addition to input variables such as excitation frequencies, dynamic or static loads or ambient temperatures, you must therefore also consider whether the element to be designed is to damp or decouple later.
Rubber-metal compounds can only be separated from each other with a great deal of effort. This makes the recycling of such products difficult. To dispose of both materials separately requires a complex recycling process with high energy input, which is hardly economically justifiable. For this reason, rubber-metal elements are usually landfilled rather than recycled. This has an impact on the company’s sustainability goals.
It is therefore advisable to ensure the longest possible service life when designing rubber-to-metal elements. The materials used should be robust and resistant to aging. Wear and tear should be minimized (if possible) at the geometric level. This not only reduces waste, but also lowers maintenance and repair costs.
Rubber-to-metal elements are by no means just complementary components to protect motors or pumps from shocks and dampen noise. There are many factors to consider in their design, from excitation frequencies to static loads to the dissipative properties of the base polymer. Those who underestimate these complexities risk failure during operation, which in the worst case can result in further damage to machinery.
Learn which factors influence your SOP!
Andrej Kisselmann is a graduate of the continuing education program in rubber technology at Leibniz University in Hanover. Since 2011, he has been working for Jäger in central product management as well as in technical sales.
Share this post!
Jäger Gummi und Kunststoff GmbH
Lohweg 1
30559 Hannover
Tel. +49 511 – 53580
Fax +49 511 – 553394
info@jaeger-gk.de
Management:
Dipl.-Ing Sebastian Jäger
Julius Jäger, M.Sc.
Hanover Register Court HRB 59798
DE 813 314 161
Petra Dirlenbach