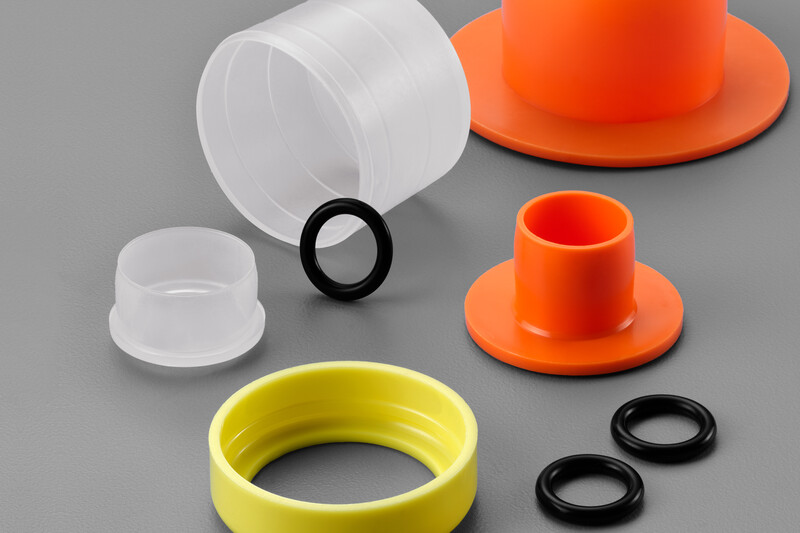
JÄGER Business Blog
WHITEPAPER
Find out which factors influence your SOP!
General-purpose rubbers are rubber grades that are suitable for most application scenarios in technology and industry. They lack the individual strengths of specialty and high-performance rubbers. However, they offer the typical material properties of elastomers at a favorable price.
Globally, general-purpose rubbers account for the largest volume share in rubber production (approx. 82 percent). Whenever a low-cost, heavy-duty elastomer product is to be manufactured, they are the first choice.
The most common rubbers in this category include:
Natural rubber forms the basis for around 40 percent of the rubber goods produced worldwide. It is obtained from the sap of the “Hevea Brasiliensis” rubber tree, whose main cultivation areas are in Southeast Asia. Unlike synthetic rubber, natural rubber is a regenerative raw material. This sustainability aspect and the low price make NR an important cornerstone of rubber production.
Originally, natural rubber was the only raw material for rubber production. Therefore, for a long time it was simply referred to as rubber. However, this has changed with the development of synthetic rubbers. The term now covers all elastic polymers from which rubber is made.
The mechanical properties of natural rubber are excellent. It has very good elasticity, high tear resistance, excellent elongation and tensile strength, and low compression set.
NR is resistant to water and dilute acids and alkalis, but should not come into contact with solvents, oils, greases, lubricants, gasoline or water vapor. The aging behavior of NR to ozone, (UV) light and weathering is to be classified as moderate to poor.
Due to its low heat build-up under dynamic load and its high tensile strength, the main area of application for natural rubber is tire construction. It is also used in automotive and mechanical engineering, for example for (vibration) dampers or as a bearing and coupling element for moving parts. High-purity NR variants are frequently processed in the food and medical sectors .
Rubber harvest from a rubber tree
Styrene-butadiene rubber was developed at the beginning of the 20th century. The aim was to develop a low-cost alternative to the (then) expensive natural rubber and to reduce dependence on raw material imports from Southeast Asia. Its starting raw materials, styrene and butadiene, can be obtained inexpensively from crude oil and natural gas, enabling low-cost production. In terms of quantity, styrene-butadiene rubber is the most commonly produced synthetic rubber.
SBR shows moderate to good resistance to dilute acids and alkalis, polar solvents and water vapor. However, it is not resistant to non-polar and aromatic solvents, oils, greases, lubricants and gasoline. Its aging behavior with respect to ozone, (UV) light and weathering is poor to moderate.
The mechanical properties of SBR are comparable to those of NR. Tear resistance, rebound resilience, abrasion resistance and compression set are at a high level. The same applies to wet slip behavior. Tear resistance is excellent if the material is reinforced.
Styrene-butadiene rubber is used primarily in tire construction due to its good wet slip properties and low abrasion. Other applications include engine suspensions, spring elements, bearings, conveyor belts and hard-wearing floor coverings.
Tires made of SBR for agricultural technology
Butadiene rubber, like styrene-butadiene rubber, originated in the early 20th century from the intention to replace natural rubber with a cheap, readily available alternative. Unlike SBR, however, BR is almost never used in its pure form. As a rule, it serves as a blending component to improve the mechanical properties of other types of rubber.
BR exhibits moderate to good resistance to polar solvents and dilute acids and alkalis. It is also characterized by high rebound resilience, very good abrasion resistance and low heating under dynamic loads.
However, butadiene rubber is not resistant to non-polar and aromatic solvents, oils, greases, lubricants and gasoline. Its aging tolerance to (UV) light, ozone and weathering is also poor to moderate. The same applies to tensile strength, elongation at break and tear resistance.
Pure BR compounds are difficult to process. They have to be blended with high proportions of fillers and/or plasticizers. In practice, therefore, they play only a minor role.
Instead, the majority of BR production goes to the tire industry as a blending component. The addition to natural rubber or styrene-butadiene rubber improves their abrasion and rolling resistance as well as elasticity. Other applications for BR-reinforced elastomers include conveyor belts, shoe soles, roll covers and bearing elements.
NR | SBR | BR | |
---|---|---|---|
Diluted acids | Moderate | Moderate | Moderate |
Diluted alkalis | Moderate | Moderate | Moderate |
Hot water | Moderate | Good | Moderate |
Polar solvents | Bad | Moderate | Moderate |
Non-polar solvents | Bad | Bad | Bad |
Aromatic solvents | Bad | Bad | Bad |
Mineral oils and greases | Bad | Bad | Bad |
Gasoline | Bad | Bad | Bad |
Ozone | Bad | Bad | Bad |
(UV) light | Bad | Bad | Bad |
Weather effects | Bad | Bad | Bad |
Resistance of general-purpose rubbers
Whitepaper: Secure the Start of Production
Learn which factors influence your SOP!
Thomas Wutke has been managing the Jäger site in Frankfurt am Main since 2020 and was previously responsible for another site. He has more than 35 years of experience in sales (KAM/B2B) of rubber and plastics as well as in project management and application development.
Share this post!
Jäger Gummi und Kunststoff GmbH
Lohweg 1
30559 Hannover
Tel. +49 511 – 53580
Fax +49 511 – 553394
info@jaeger-gk.de
Management:
Dipl.-Ing Sebastian Jäger
Julius Jäger, M.Sc.
Hanover Register Court HRB 59798
DE 813 314 161
Petra Dirlenbach