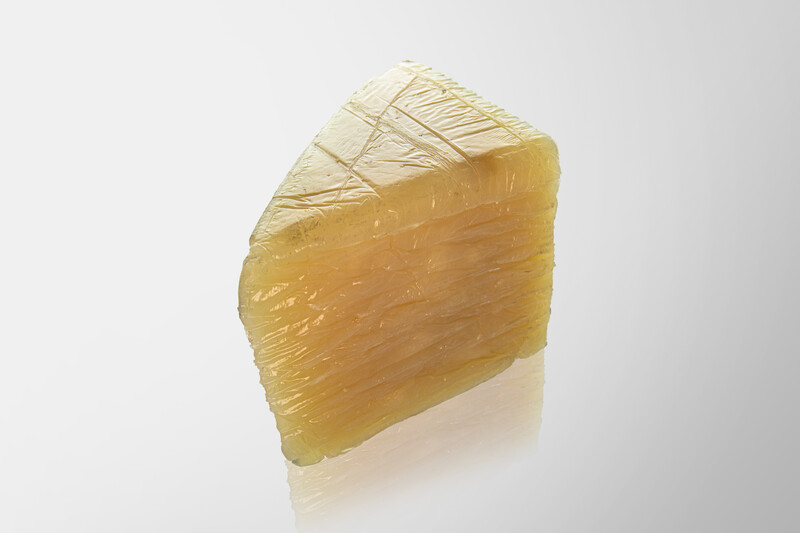
JÄGER Business Blog
WHITEPAPER
Learn how agricultural engineering can meet most of the current challenges
Seals are often treated stepmotherly in product development. Whenever there is a risk of foreign substances penetrating or escaping somewhere, the design department plans a seal. Few designers give much thought to the specific design of the component.
This approach can cause problems because the material has a major impact on the reliability and service life of a seal. If it is made of the wrong material for the application, the seal will fail sooner or later and, in the worst case, shut down the entire plant. The consequences are production downtimes and high follow-up costs. Designers should therefore ensure that they select the right gasket material in advance.
Unfortunately, there is no universal material that covers all potential applications. Each material has certain properties that have different effects depending on the scenario.
Some materials are extremely resistant to mechanical stresses and feature good compression set and high tear strength. Others are highly temperature resistant and retain their properties even in extreme heat or cold. Some materials are insensitive to various substances or media with which they come into contact: Grease, mineral oil, gasoline, solvents, various acids or bases, etc. Still others are resistant to UV light or ozone and do not become porous under their influence. There are also differences in terms of electrical conductivity. Some materials have an insulating effect and others are electrically conductive.
Depending on the material, the properties of a seal can vary greatly. The challenge is to select the right one from the quantity of available materials. There is a suitable material for every scenario.
If you want to know which materials are resistant or susceptible to which media, you can refer to our resistance list for elastomers.
The media with which a seal regularly comes into contact depends on the area of application. It is therefore enormously important to analyze the general conditions thoroughly before selecting the gasket material. A large part of the contact media results from the primary area of application. For example, a gasket in a vehicle engine must be resistant to gasoline and machine oil and tolerate heat well.
However, it is risky to derive gasket material requirements from design drawings alone. The context of use is also relevant.
For example, a machine that is operated outdoors is often exposed to direct sunlight. This means that its seals must not become porous when exposed to UV light and ozone. The expected outdoor temperatures also play a role. If the machine is outdoors during the winter months, its seals must be able to withstand sub-zero temperatures. In summer, on the other hand, some locations can reach relatively high temperatures.
Sealing ring when used incorrectly and correctly
However, the requirements placed on a seal are not necessarily static. It is entirely possible that the area of application of a machine or system will change over time.
In such cases, all seals would actually have to be put to the test again. However, not all companies take the trouble to analyze their equipment conceptually when the area of application changes. Often, the analysis remains superficial. This can have a negative impact on the service life of the seals.
The decision in favor of a particular sealing material does not take place in a vacuum. Apart from resistance, there are numerous other relevant properties.
Material costs in particular often play a major role. Some companies deliberately opt for seals that have a shorter service life but are significantly less expensive. Financially, it can be well worth replacing a gasket on a regular basis rather than using a long-lasting but more expensive one. Precisely because seals are not part of the primary intended use of a machine or system, they regularly suffer as costs are reduced.
However, using lower quality seals can cause problems. For example, the service life of the machine or system also depends on the reliability of the seal material. If foreign material leaks or penetrates in the wrong place, functionality or operational safety may be compromised. This can result in high repair costs and production downtime.
If the problem occurs with customers, the company’s reputation may even suffer. Designers should always consider this risk when choosing a sealing material.
Many designers regard seals as simple auxiliary materials and pay too little attention to them. However, there are numerous aspects to consider when selecting a sealing material. If the material is suitable for the area of application of a machine or system, this has a positive effect on its service life. However, if the design chooses the wrong material, the seal has to be replaced more frequently — the risk of machine failure increases. It is therefore worthwhile to consider more than just cost when choosing a seal material.
Learn how agricultural engineering can meet most of the current challenges
Share this post!
Jäger Gummi und Kunststoff GmbH
Lohweg 1
30559 Hannover
Tel. +49 511 – 53580
Fax +49 511 – 553394
info@jaeger-gk.de
Management:
Dipl.-Ing Sebastian Jäger
Julius Jäger, M.Sc.
Hanover Register Court HRB 59798
DE 813 314 161
Petra Dirlenbach