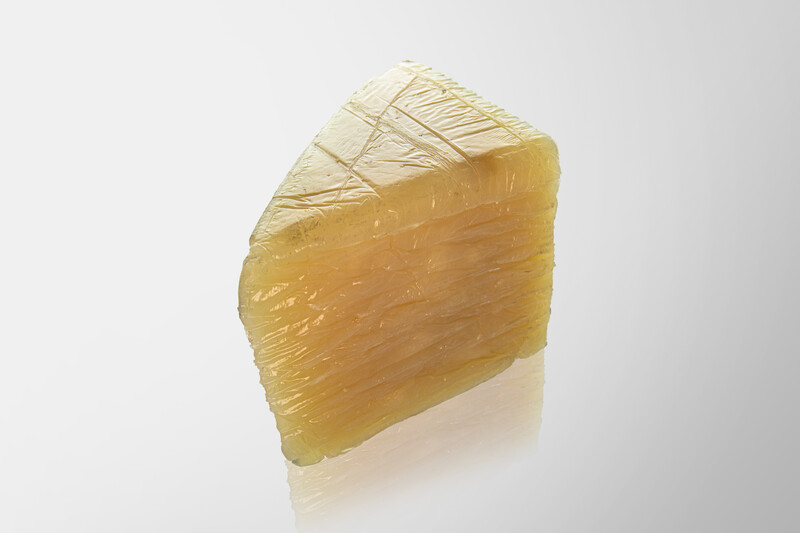
JÄGER Business Blog
WHITEPAPER
Find out which factors influence your SOP!
The Corona pandemic has shown how fragile the supply chains of modern companies really are. Of course, the vulnerability of branched supply chains to disruption is not a new insight. However, over the past two years, the global economy has experienced for the first time what happens when the worst happens. In light of this wake-up call, companies should ask themselves whether they want to continue sourcing their rubber and plastic molded parts from the Far East.
In most companies, supply chain management is price-driven. If several suppliers offer goods of comparable quality, purchasing usually opts for the less expensive supplier. As a result, a great many producers source their plastic and elastomer molded parts from Asia, a region characterized by a robust industry and low raw material and labor costs.
However, with the monetary benefits that sourcing from Asia offers come some risks. For example, basic delivery times are significantly higher than those of European suppliers. An order placed by ocean freight may well be three months in transit before it arrives in Europe.
In addition, the long transport route offers more opportunities for unforeseen events that can prevent timely delivery. On a voyage lasting several months, there is a much greater chance that bad weather or congested ports will cause delays. In addition, shipments of goods pass through several bottlenecks on their way from Asia to Europe, where disruptions can have serious consequences. Just think of the blockade of the Suez Canal in March 2021.
Then there are geopolitical risk factors. Punitive tariffs or import restrictions imposed due to trade disputes or diplomatic incidents can also delay or even block shipments of goods, often with only a few weeks’ notice.
In a stable economic situation, these disadvantages are compensated by lower purchase prices. In times of crisis, however, this changes.
The economic impact of the Corona pandemic cannot yet be precisely assessed. What is certain, however, is that some sectors have suffered greatly from the crisis. Among other things, sales in the catering, tourism and local transport sectors have fallen sharply, which has also had an impact on their suppliers and service providers. At the end of this causal chain is the raw materials industry, which has also suffered a drop in sales and has reduced its extraction or production volumes accordingly.
Since summer 2021, the number of newly reported corona cases has been declining worldwide. Most industrialized countries are experiencing an economic upswing. As a result, demand for raw materials and supplies is currently rising sharply, which in turn is driving up prices. More serious, however, is the lack of availability of certain raw materials. Thanks to the enormous demand, some resources (steel or plastics, for example) are almost impossible to obtain. And if they are, the supplier often cannot guarantee a fixed delivery date.
Development of elastomer price indices (Source: www.wdk.de)
For European manufacturing companies whose production planning depends on on-time delivery of raw materials and components, this situation is a major challenge. This is especially true for organizations that source their rubber and plastic molded parts from Asia. They lack the flexibility to find another solution at short notice if a supplier has delivery problems.
It is true that it is possible to order goods from the Far East with longer lead times, thus reducing the negative impact of delays. However, this is only possible if the company has sufficient storage capacity, which on the one hand involves costs and on the other hand contradicts the basic idea of modern supply chain management to move the warehouse to the street.
In the course of this, European suppliers are currently coming more into focus. Thanks to their geographical proximity, their basic delivery times are significantly shorter than those of Asian manufacturers. The inner-European rail or highway network has no significant bottlenecks that could form a bottleneck. In addition, there are no border controls within the Schengen area. All these factors ensure that the delivery reliability of European suppliers is significantly higher.
Supply chain management is always also a question of risk affinity. Complex supply chains that include raw materials, materials and components from all regions of the world reduce production costs and thus improve competitiveness. However, they also entail high risks. If a major disruption does occur, the companies affected find it difficult to take countermeasures at short notice. Working with local suppliers, on the other hand, is much safer, but also involves higher costs.
Ultimately, each company must decide for itself how it wants to set up its supply chain management. Some will continue to source their resource requirements from the Far East as they face high price pressure. For others, it makes sense to switch to European suppliers to gain more certainty. It is only important that manufacturing companies are aware of the risks that purely cost-oriented supply chain management entails. The last two years have shown what can happen in the worst case.
Whitepaper: Secure the Start of Production
Learn which factors influence your SOP!
Share this post!
Jäger Gummi und Kunststoff GmbH
Lohweg 1
30559 Hannover
Tel. +49 511 – 53580
Fax +49 511 – 553394
info@jaeger-gk.de
Management:
Dipl.-Ing Sebastian Jäger
Julius Jäger, M.Sc.
Hanover Register Court HRB 59798
DE 813 314 161
Petra Dirlenbach