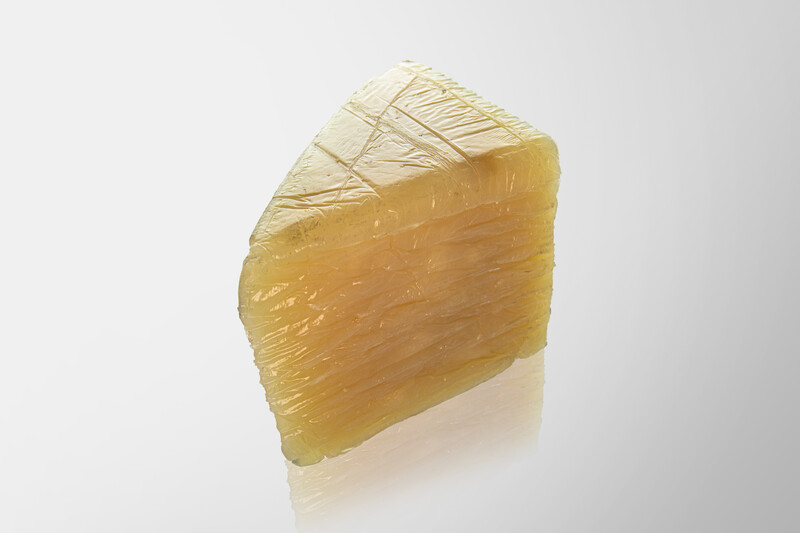
JÄGER Business Blog
WHITEPAPER
Find out which factors influence your SOP!
There are many reasons for project delays in both elastomer and plastics production. Delivery problems along the supply chain are often to blame. Particularly at the start of a project, there is a time factor that only a few customers have in mind, although it accounts for a non-negligible part of the lead time before the start of series production: toolmaking. This is much more complex for both rubber and plastic products than it might seem. If customers underestimate the manufacture of the tool during development, this puts on-time project completion in jeopardy.
The geometry of the molding tool must exactly match the dimensions of the molded parts to be produced, including necessary tolerances. For this reason, a separate tool must be manufactured for each project according to a special customer drawing, which also includes design, manufacturing and transport. In a sense, tooling is a project within a project and the most important link along the manufacturing chain for a functioning part. Due to the large scale of the manufacturing process, it is obvious that it often results in delays.
There are four major influencing factors that often delay the on-time delivery of the mold (and thus the start of production of the molded part):
As a rule, customers create a design drawing of the required molded part before contacting a production partner such as Jäger — Gummi und Kunststoff. However, this drawing is often focused on the geometric requirements of the finished component, not on its production. As a result, customer specifications are often not designed for production.
Common problems include missing draft angles or missing radii. Other errors are production-specific and escape designers who are not familiar with the material.
One example is the different flow behavior of rubber and plastic. Rubber is injected cold into the mold and then heated or vulcanized, while plastic is injected hot and cools/solidifies in the mold. In both cases, the raw compound behaves fundamentally differently during manufacturing. However, the subtleties are found within the materials used. Each material — whether plastic or rubber — flows differently during the injection process. Here, know-how is essential in order to select the type and method of gating, as otherwise various defects can occur in the material of the end product, e.g. visible flow defects.
Development at Jäger
Only a few producers still manufacture tools in-house these days. Instead, they usually outsource tasks beyond their own core competencies to service providers. This is also the case in toolmaking. As a rule, the manufacturing partners are located within Germany. Working with domestic service providers simplifies communication and reduces the organizational effort that results from different legal frameworks and logistics requirements.
In some projects, however, the cost pressure from the customer is very high. In such cases, it makes sense to outsource toolmaking to low-wage countries. China is often chosen because of its robust steel industry and lower raw material costs.
The quality of the tool is quite comparable with German manufacturers. However, the coordination effort is correspondingly higher. Especially if the molding producer does not have its own local branch and communication takes place across different time zones. Although coordination with German partners also affects the timing of the manufacturing project, in an international context with complicated projects this delay is significantly higher.
Another factor is logistics. If the mold is produced by an external partner, transport can lead to delays depending on the situation. Here, too, it depends on whether the molding producer is working with a local or an international moldmaker.
If the mold is manufactured in Germany or a neighboring EU country, transportation usually takes relatively little time and can often be handled by in-house capacity. However, in some cases, delays can occur due to weather or traffic. If the toolmaker manufactures in Asia, the situation is different. Then the transport may cost a lot of time. Transporting the tool by air freight is relatively quick, but not always possible. Especially when there is high cost pressure, many companies switch to cheaper transport routes, such as sea freight or rail transport. The delivery time is correspondingly longer.
Tools for molded part production are precision instruments. Even slight deviations from the design specifications, especially with tight tolerances, can render the articles produced unusable. For this reason, the tool is thoroughly checked before production starts.
Several parties are involved in this task. First, the toolmaker himself checks whether he has implemented all specifications correctly. Then, the rubber producer re-measures specific dimensions before installing the mold in the production line and setting it up on the injection molding machine. The customer of the molded part is not directly involved in this process. However, he checks the correctness of the mold indirectly by inspecting the samples produced with it and checking the initial sample report.
Measurements in particular take time because they have to be very precise. Special instruments are usually used for this purpose, which can identify the smallest inaccuracies.
Mold making is an integral part of any injection molding manufacturing project, whether rubber or plastic. Most customers are aware that an injection mold is needed. However, they underestimate how much effort lies behind its manufacture. An injection mold is not a standard component, but a precision tool that is made individually for each job.
Mold manufacturing is a project within a project. It goes through the same process as any other production, from manufacturing to release. All of this takes time. Building a tool cannot be shortened or accelerated. That’s why it’s important to factor it into project scheduling right from the start.
In the best case, companies contact a rubber manufacturer during development who is familiar with the material and can contribute empirical values. This makes scheduling much more robust and minimizes potential problems and errors.
Whitepaper: Secure the Start of Production
Learn which factors influence your SOP!
Share this post!
Jäger Gummi und Kunststoff GmbH
Lohweg 1
30559 Hannover
Tel. +49 511 – 53580
Fax +49 511 – 553394
info@jaeger-gk.de
Management:
Dipl.-Ing Sebastian Jäger
Julius Jäger, M.Sc.
Hanover Register Court HRB 59798
DE 813 314 161
Petra Dirlenbach