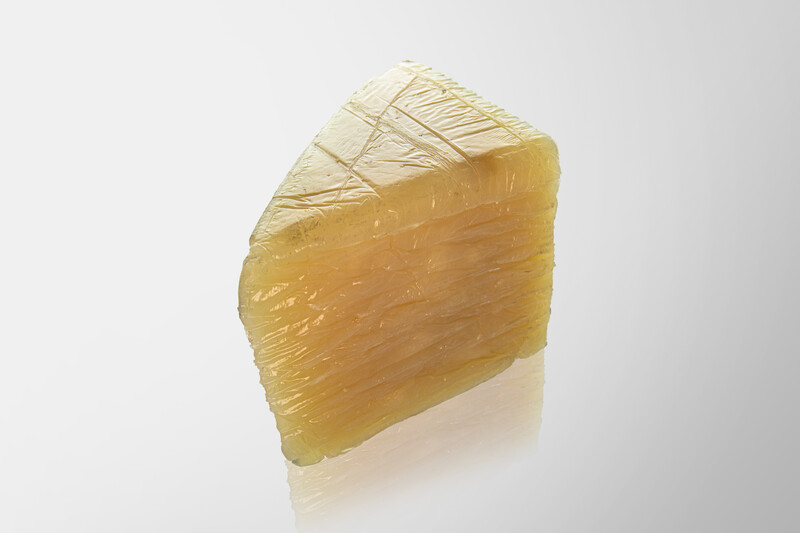
JÄGER Business Blog
WHITEPAPER
Learn how agricultural engineering can meet most of the current challenges
Wherever screening and sorting is required, rubber stars are in use. The materials conveyed come from a wide variety of sources — for example, recycled material, organic matter from composting, or stony debris. In order to achieve the longest possible service life, they should be made of a material that is optimally suited for the respective area of application. Jäger can rely on a broad base of successful projects and make recommendations based on experience.
Two main material groups have become established for industrial rubber stars: Nitrile rubber (NBR) and thermoplastic elastomers, mostly urethane-based (TPU). Both are characterized by different properties in production and practical use.
Nitrile rubber is a synthetic rubber with a low purchase price and high resistance to water, oils and greases. However, designers have to make slight concessions when it comes to abrasion. Good compounds show excellent values here, but these are higher than those of PU plastics.
Thermoplastic polyurethane is available in two variants: ether-based and ester-based. Both materials have similar characteristics, but differ specifically in terms of mechanical abrasion and their resistance to hydrolysis. Ether-based thermoplastic polyurethane (or ether TPU) is resistant to water and microbes, but has less good mechanical properties in comparison, especially somewhat higher abrasion. For ester-based TPU (or also ester TPU), the behavior is reversed.
Which material is more suitable for the production of stars for screening depends on the project budget, the production volume, the actual requirements and the geometry of the stars.
If we look from the calculatory side with regard to the production volume, the following point becomes clear: Vulcanizing molds for NBR components are less expensive than those used for TPU molded parts in the injection molding process. However, the process costs in TPU injection molding are typically lower for plastics above a certain series size (depending on the geometry). For small series, NBR is therefore more suitable because the mold recoups very quickly. For large series, on the other hand, injection-molded TPU is preferable. For the sake of completeness, PU-cast stars should also be mentioned. Here, the mold costs are also low, but the unit costs are higher than for the comparable product made of NBR. The biggest disadvantage here, however, is the long cycle time per product.
The mechanical and chemical properties of the materials also play a major role in material selection, especially hydrolysis resistance. If the feed material is potentially moist (e.g. organic material such as prunings or compost), stars for screening made of NBR or ether TPU are useful. These are less prone to molecular damage when in contact with water and are less susceptible to microbes. For oily feed materials (e.g., seeds), stars for screening made of NBR are well suited, but certain TPU compounds can also be oil-resistant.
However, the specific chemical and mechanical requirements for the star material are often difficult to define. In forestry, for example, the extent to which the feed material is moist or dry depends on the weather, and oils can also leak out if seeds happen to be present.
In addition, desired service life influences material selection. High abrasion means that the stars for screening wear out more quickly and thus lose their efficiency. They must be replaced at shorter intervals, which increases maintenance costs. However, abrasion, and thus service life, depends on the feed material. A screen deck that handles abrasive materials (e.g., boulders) will wear out faster than one that handles soft wood. In some cases, it may also make sense to reinforce stars for screening with metal to make them more resistant (so-called “armored stars for screening”).
Furthermore, the geometry of the stars is relevant for the material selection, especially wall thickness and weight. The wall thickness plays a role because it influences the cycle times during production. Solid NBR stars for screening have to be heated for a longer time period until the vulcanization of the material is completed than thin-walled versions. Vice versa, a TPU star for screening must be cooled in the injection molding process so that the end product retains its shape. A decision must be made on a case-by-case basis.
Functionality of a screen deck
Choosing the right material for a screen deck essentially depends on four key questions:
1. What is the budget for the project?
2. How large do you want the screen deck to be?
These two questions are related, as they both involve the monetary side of the manufacturing project and they are often correlated. If it is a single screen deck with only a few stars for screening, NBR is the better material because of the cheaper mold. Furthermore the increased process costs are somewhat relativized with low production volumes. In the case of large or multiple screen decks, on the other hand, TPU is to be preferred, since the mold recoups over time and the low process costs come into sharper focus.
3. Which material is conveyed?
The feed material influences which media the stars for screening come into contact with, which again has consequences for the material selection. For wet materials, NBR or ether TPU are preferable because of their hydrolysis resistance. With dry material, on the other hand, Ester-TPU is the better choice, as the better mechanical properties get more important. If, on the other hand, the feed material contains oil, the stars for screening should either be made of NBR or of certain TPU compounds specially designed for oily materials.
4. What does the geometry look like?
The thicker the wall, the longer the cycle per unit produced in general. In this case, it must be decided on a case-by-case basis, depending on the material and production volume, which production method is suitable.
These questions give a direction for the main influences. However, the choice of material is not always clear. It happens that different materials seem to do the job; for example, if a large screen deck with massive stars for screening and long service life is desired, which is to process moist cuttings that sometimes also contain oily seeds — and all this with a low project budget. In such a case, it is advisable to call on the consulting services of a rubber and plastics producer to select the right material in each individual case.
On the surface, material selection for stars for screening is quite simple, as there are often only three materials to consider: nitrile rubber (NBR) and ether- and ester-based thermoplastic polyurethane (TPU). All three differ in terms of their cost structure and their chemical and physical properties. Which material is most suitable always depends on the context. It is therefore advisable to analyze the application area of the screen deck in detail before selecting the material.
Learn how agricultural engineering can meet most of the current challenges
Share this post!
Jäger Gummi und Kunststoff GmbH
Lohweg 1
30559 Hannover
Tel. +49 511 – 53580
Fax +49 511 – 553394
info@jaeger-gk.de
Management:
Dipl.-Ing Sebastian Jäger
Julius Jäger, M.Sc.
Hanover Register Court HRB 59798
DE 813 314 161
Petra Dirlenbach