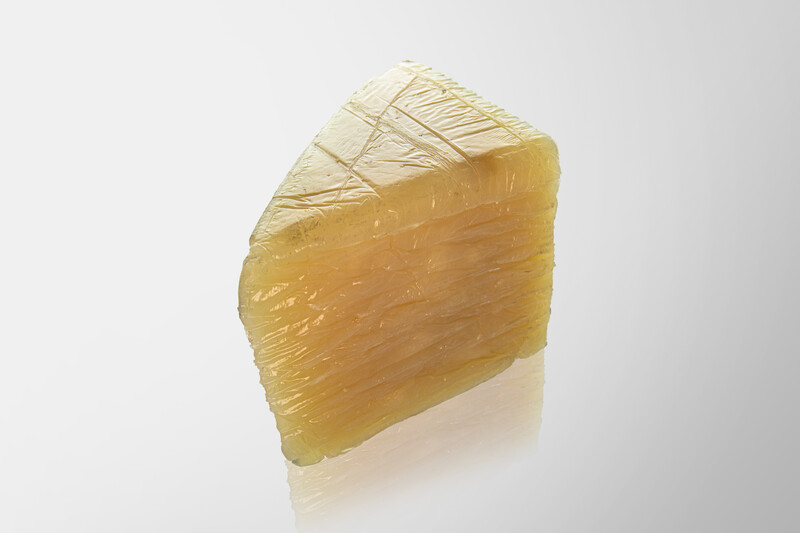
JÄGER Business Blog
How manufacturing companies should react.
WHITEPAPER
Find out which factors influence your SOP!
The global shortage of raw materials has led to supply bottlenecks across all sectors. The reasons for this are, on the one hand, rising demand as a result of the pandemic-related economic downturn and, on the other, the continuing reduced production capacities of raw material suppliers. This effect has been exacerbated by recent disruptions to global supply chains, such as the blockade of the Suez Canal or the temporary closure of the container terminal at the Chinese cargo port of Ningbo-Zhoushan.
Currently, 78 percent of medium-sized companies in Germany are affected by material shortages. This applies not only to wood and steel, but also to the rubber and plastics industries.
How can production companies respond to this situation? What short- and medium-term solutions are there to overcome this crisis? And what can decision-makers do to ensure material supplies despite shortages?
Short-term measures are relatively difficult to implement because the shortage of raw materials is a far-reaching phenomenon. Affected companies cannot simply switch to another manufacturer, because supply problems are basically universal. In addition, competitors are also on the lookout for raw materials and input materials, which further fuels the raw materials market.
One possible solution is to evaluate alternative materials that may be less in demand. These may be generic variants of the same material, such as a different brand, or materials with slightly different characteristics.
In the course of material selection, for example, design often crosses materials off its list that are not considered because of minor issues. In most cases, these fabrics still meet the primary requirements. They are just not optimal for the intended use. In the current situation, it makes sense to give these materials a chance.
Unfortunately, alternative materials are not a short-term option for all industries. In the food or pharmaceutical industries, for example, materials go through complex approval processes with multiple rounds of testing before they are released for production. Although the release of alternative materials is possible in principle, it can take up to six months. In addition, there is no guarantee that the new options will still be available at the end of the evaluation process.
Despite the competitive situation, some manufacturing companies are trying to counter the crisis through cooperation. It happens continuously that someone urgently needs material A and at the same time has a surplus of material B in stock. In this case, it is possible to barter with other companies that are in a similar situation.
However, finding partners can be relatively time-consuming – especially if those responsible lack the appropriate contacts. For this reason, various digital trading platforms for raw materials have now become established on which companies can search for resources and offer them for exchange. Currently, these offerings are still manageable, but it may be worthwhile to take a look.
Im Zweifelsfall ist es ratsam, den Kontakt mit Ihren Lieferanten zu suchen. Diese wissen am besten, welche Materialien wann und zu welchem Preis verfügbar sind, und können Sie entsprechend beraten. Melden Sie sich bei uns, falls Sie weitere Informationen benötigen.
In the medium term, companies have a little more leeway in procurement. Raw materials and intermediate products are certainly available, but often with long delivery times (currently around six months for rubber and plastics). If you know now what material requirements can be expected in six months’ time, you can place orders early and secure your supply of raw materials.
Framework agreements are a good way of doing this. In these, the supplier undertakes to provide a certain quantity of goods within an agreed period. At the same time, the customer undertakes to purchase these goods. The advantage for both sides is that they can enter into this interaction on a long-term basis.
One possible solution to the shortage of raw materials in production is to pre-order rubber and plastic components to secure medium-term requirements. However, keeping products in stock for a longer period of time requires corresponding storage capacities, which are associated with costs. This is where framework agreements come into play. They offer both sides legal security and thus enable production to be shifted into the future
Logistic center
A framework agreement offers both sides legal security and gives them enough leeway to work out the cooperation more efficiently. The supplier can anticipate that the customer will buy a certain quantity of goods from him and plan his production accordingly. The customer, in turn, does not have to provide additional storage capacity, because the timely delivery of his required components is contractually fixed.
The advantages of framework agreements in the context of pandemic raw material shortages are:
However, companies should not rely 100 percent on the last point. The market is still tight and further price increases are to be expected. In view of this, rubber and plastics suppliers may be forced to adjust their prices as well in order not to incur losses. In case of doubt, it is advisable to agree a price escalation clause to contractually safeguard this point.
Responding to the current shortage of raw materials and the associated supply bottlenecks is relatively difficult. Modern supply chains are not designed to respond flexibly to disruptions and therefore do not offer inherent countermeasures. The best way out of this situation is to intensify contact with suppliers and work together to find a solution. After all, everyone is in the same boat.
It is also important to learn from the current crisis. The COVID 19 pandemic has shown how fragile the procurement strategies of modern business really are. The current bottlenecks should be a reason to revise one’s own supply chain management and emerge stronger from the crisis. Acting with foresight is the decisive keyword in this context.
Whitepaper: Secure the Start of Production
Learn which factors influence your SOP!
Share this post!
Jäger Gummi und Kunststoff GmbH
Lohweg 1
30559 Hannover
Tel. +49 511 – 53580
Fax +49 511 – 553394
info@jaeger-gk.de
Management:
Dipl.-Ing Sebastian Jäger
Julius Jäger, M.Sc.
Hanover Register Court HRB 59798
DE 813 314 161
Petra Dirlenbach