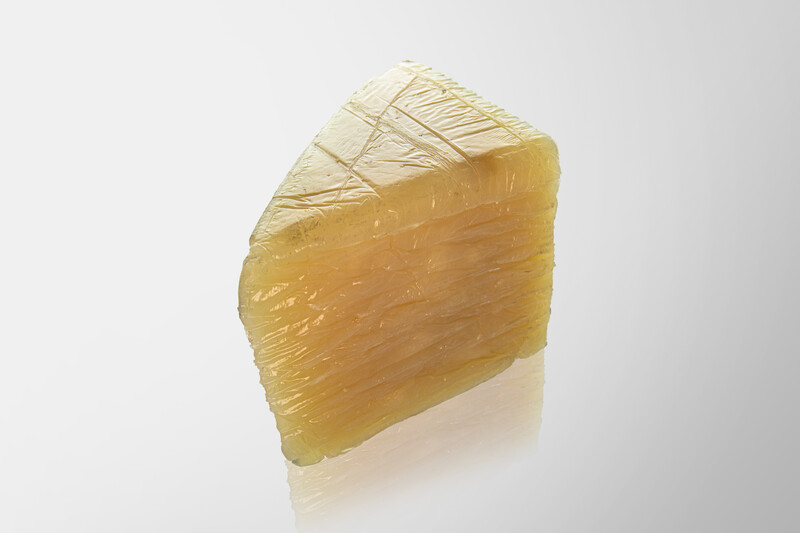
JÄGER Business Blog
WHITEPAPER
Find out which factors influence your SOP!
Rubber and metal are among the material groups found in almost all industrial products. Knowing their differences and similarities is essential for any manufacturing company. However, few organizations can demonstrate competency in both areas.
Most designers come from the metal world. That is where their core competencies lie. They often have little experience with other materials. Yet it is well worth knowing the differences and similarities between elastomers and metals so that they can be combined as efficiently as possible.
Rubber is an elastic material that expands and contracts and reacts to external influences. This is an advantage when it comes to sealing and damping, because rubber can flexibly adapt to dynamic forces. In construction, on the other hand, this property can pose a problem.
The elastic characteristics of rubber limit the possible tolerances in production. Elastomers cannot be manufactured as precisely as metals. The properties of the material do not allow this. In metal construction, for example, filigree geometries are possible that are a fraction of a millimeter wide. Just think of knife blades. In elastomers, on the other hand, a width of 0.5 mm is possible with a great deal of effort.
Below that, the production of rubber can no longer be carried out with process reliability.
Many designers are used to tolerances in the hundredth or thousandth range and expect the same from rubber molded parts. For this reason, producers often receive inquiries about geometries that cannot be realized. This leads to additional technical arrangements and adjustments that can drag out the development project and often have a negative impact on costs.
Another factor concerns the vulcanization process. Very fine geometries require optimum flow behavior in order to guide the raw rubber into all corners of the mold. Even slight premature vulcanization can mean that the raw rubber can no longer fill the filigree recesses of the mold.
Under certain circumstances, the temperature of the preheated mold may already be sufficient to influence the flow behavior of the raw rubber in such a way that the geometry can no longer be realized. It would be possible to allow the mold to cool down completely, but this would have a negative effect on cycle times and drive up the price of the molded articles significantly.
Be careful not to design too filigree geometries for rubber molded parts. In many cases, these cannot be realized with an elastic material. Experiences from the metal sector cannot be transferred 1:1 at this point.
Compared with metal components, the requirements analysis for rubber molded parts is more complex and extensive. Elastomers are less standardized than metals. Their material properties depend to a large extent on the additives that are mixed into the raw material. Only in rare cases is it possible to cover the desired properties of a rubber component with a standard compound. Rubber is a flexible material that must always be adapted to the particular application.
However, this flexibility also offers room for error. There are many variables to consider when selecting an elastomer. If these are specified incorrectly, the end product may not have the desired properties. This aspect distinguishes elastomers from metals, which inherently have almost all of the key material properties.
For this reason, requirements analysis is a top priority when specifying a rubber molded part. The production partner must know, for example
These specifications are an important prerequisite for material selection, because they determine the exact composition of the rubber compound.
The requirements analysis for elastomers is much more extensive than you are used to in the metal sector. Describe the intended use of the molded part as precisely as possible in your specifications and be prepared for queries.
In terms of processing, metals offer more leeway than elastomers. Rubber molded parts are usually produced by injection molding in a mold. Simple geometries can be cut or punched from sheets and profiles extruded. Subsequent machining is possible only to a limited extent. This is where elastomers differ from metals, which are mainly machined.
Take, for example, a pipe that is to have a groove inside. With a metal pipe, production can simply mill the groove into it. This is not possible with a rubber pipe. Here, the groove must be taken into account during the design stage and the tool must be designed accordingly. The finer the groove is to be, the more difficult this task is, because with very acute angles or filigree geometries, the molded part can be damaged when it is removed from the mold. The design must also take this into account during product development.
Keep the manufacturing process in mind when designing a rubber molded part. Elastomers cannot be machined in the same way as metals. For very pointed or fine geometries, it is advisable to consult material experts.
The differences between rubber and metal primarily concern the degree of standardization and flexibility in product development. Rubber is an elastic material perfectly suited for damping and sealing. This advantage comes at the price of a lower degree of precision, which translates into lower tolerances and difficulties in realizing filigree geometries. At the same time, rubber must always be adapted to its field of application. This process requires a thorough analysis of requirements.
In practice, these differences are mainly relevant for design. Elastomers and metals do not compete with each other. They complement each other. Almost every industrial product contains a combination of rubber and metal. Therefore, the design should be familiar with both materials.
Whitepaper: Secure the Start of Production
Learn which factors influence your SOP!
Andreas Fröhner has been a field sales representative at Jäger’s Hamburg location since 2001. The qualified technical business economist originally comes from the automotive sector and has broad knowledge of the entire rubber and plastics range.
Share post now!
Jäger Gummi und Kunststoff GmbH
Lohweg 1
30559 Hannover
Tel. +49 511 – 53580
Fax +49 511 – 553394
info@jaeger-gk.de
Management:
Dipl.-Ing Sebastian Jäger
Julius Jäger, M.Sc.
Hanover Register Court HRB 59798
DE 813 314 161
Petra Dirlenbach