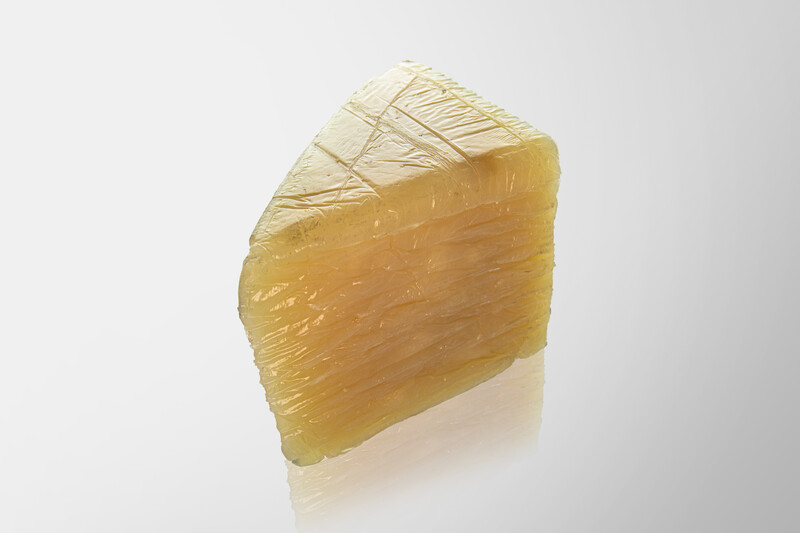
JÄGER Business Blog
WHITEPAPER
Find out which factors influence your SOP!
Seals are often considered a means to an end in design. Yet the design and selection of rubber or plastic seals can be highly complex. There are a lot of factors that affect the performance and life of a seal, and if it is designed incorrectly, it will fail sooner or later. Under certain circumstances, this can damage the machine or system in which the seal is installed.
To prevent this, it makes sense to take a detailed look at the general conditions before selecting or developing a seal. The following seven questions will help you with this analysis:
The operating temperature is one of the most important general conditions in sealing technology. If a component is operated outside its optimum temperature range, its physical properties may change. This applies to both downward and upward deviations.
The temperatures to which a seal is exposed depend on several factors, e. g. the ambient temperature. Here, the room or outside temperature plays a role, but also the conditions inside a machine or system. For example, the temperatures inside an engine are different from those outside the vehicle. The temperatures of the media with which the seal comes into contact should also be taken into account. For example, a pipe that transports water vapor can become very hot, regardless of its location.
There is also the question of temperature fluctuations. Is the temperature constant or do peaks occur? Especially frequent changes between hot and cold can damage a seal in the long run.
The chemical resistance of a seal depends on the materials with which it comes into contact. On the one hand, the substances that have a permanent effect on the seal must be taken into account (as a rule, these are also the substances against which the seal is to be sealed), for example acids, bases, gasoline or solvents. On the other hand, designers should also consider substances with which the seal only comes into contact temporarily, such as cleaning agents or disinfectants.
It is also important to note that the contact media can influence the temperatures to which the seal is exposed. For example, if a machine is regularly cleaned with hot steam, all its components must be resistant to heat and steam, even if this is not relevant throughout.
With regard to the mechanical properties of a seal, it is important whether it is subjected to static or dynamic stresses. For example, a flat seal at rest must meet different criteria than a bellows seal that is constantly in motion. The intensity of the stress should also be taken into account in the design considerations. For example, does the seal have to withstand slight movements or is it exposed to strong vibrations? This will affect the seal material, as well as the optimum shape of the component.
Machines that are operated outdoors are exposed to UV radiation during the day and often to ozone pollution in the summer months. Both of these factors negatively impact the life of many rubber and plastic compounds. Therefore, if the seal is intended for outdoor use, care should be taken when selecting the material to ensure that it is resistant to UV light and ozone.
If a seal is located inside a machine or system, its appearance is usually secondary. However, if it is a visible part, aesthetic factors may become relevant depending on the application. This includes, but is not limited to, gap dimensions, discoloration, and visual effects resulting from the manufacturing method. Here are some examples of unsightly features:
Waterjet cutting
Seals used in the medical and food industries in particular must meet strict requirements, certifications and quality standards. This primarily affects the choice of materials. Under no circumstances may a seal release harmful substances to food or medicines, regardless of the environmental factors. In some scenarios, it makes sense to manufacture seals from detectable materials so that detached particles can be identified and removed more easily if necessary.
The planned quantities of a seal are primarily relevant to the type of production. In the case of small production quantities, it makes sense to cut the molded parts by plotter or waterjet. If the quantities increase, on the other hand, tool-based processes (e.g. punching) make more sense. The break-even point depends on geometry and material and must be determined individually. However, the envisaged quantities should be taken into account early on in the product development process so that the seal can be designed to meet production requirements.
The development and selection of a seal is much more complex than it appears. Many factors play a role, from the ambient temperature to mechanical stresses and prescribed certifications to the appearance of the component. All these aspects must be taken into account when selecting or developing a seal. It is therefore important to carry out a detailed analysis of the framework conditions at the beginning.
Whitepaper: Secure the Start of Production
Learn which factors influence your SOP!
Share this post!
Jäger Gummi und Kunststoff GmbH
Lohweg 1
30559 Hannover
Tel. +49 511 – 53580
Fax +49 511 – 553394
info@jaeger-gk.de
Management:
Dipl.-Ing Sebastian Jäger
Julius Jäger, M.Sc.
Hanover Register Court HRB 59798
DE 813 314 161
Petra Dirlenbach