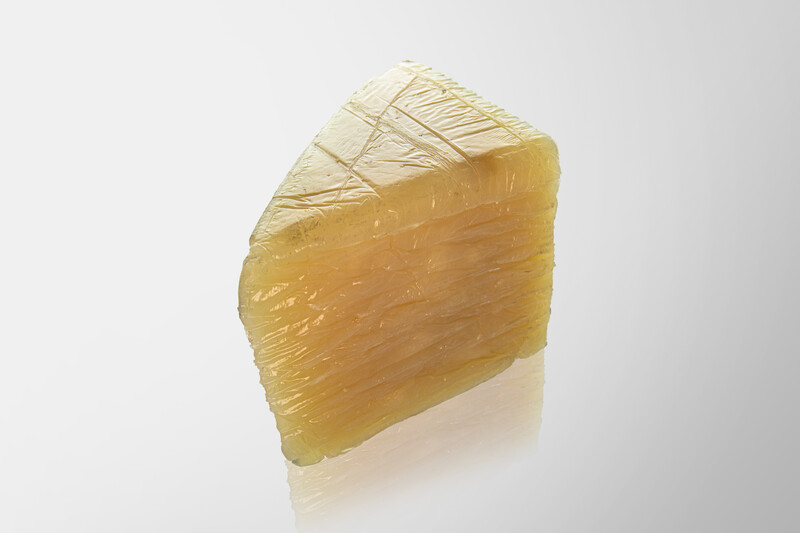
JÄGER Business Blog
raw material shortages in Germany
WHITEPAPER
Find out which factors influence your SOP!
Beyond the terrible humanitarian consequences, the war in Ukraine has also hit global supply chains hard. Production capacities in the contested areas have been impaired, and political sanctions are also hampering trade with Russian suppliers. This is exacerbating the ongoing shortage of raw materials and posing problems for the manufacturing sector. The plastics and rubber processing industries are also affected.
The question is: How should companies respond to this shortage of raw materials and what is the way out of the crisis?
The Ukraine conflict is not only affecting the production of crude oil, natural gas, steel and wheat. Russia is also one of the most important suppliers to the global rubber industry. Russian suppliers of polybutadiene (BR) and isobutene-isoprene rubber (IIR) each have double-digit market shares. In 2021, Russian companies supplied about 550,000 tons of carbon black and 240,000 tons of synthetic rubber to the European Union, according to statistical data from Eurostat.
Purchasing cannot replace such volumes of raw materials overnight. If supply relationships are permanently interrupted, supply bottlenecks and significant price increases are to be expected.
At the same time, energy costs are skyrocketing, as Russia and Ukraine have so far met a large share of European demand for oil and natural gas. Western sanctions and damage to Ukrainian infrastructure are significantly limiting this supply. Alternative suppliers such as the USA, Norway or Qatar can only fill these gaps to a limited extent.
The resulting price increases are hitting the energy-intensive rubber industry hard and driving up production costs. Production losses cannot be ruled out either if price increases jeopardize profitability and there is a shortage of production-relevant raw materials.
The rubber processing industry has not yet fully recovered from the pandemic-related raw material shortages. The crisis in Eastern Europe is further heating up the situation on the raw materials market, as supply relationships with Ukrainian and Russian trading partners have been cut off.
In addition, the perspective has changed. Previously, raw material shortages were the result of an imbalance between supply and demand, due to the demand peak of a global economy recovering from the financial impact of a pandemic. In such a situation, suppliers may be able to service their customers’ orders, but not within the agreed timeframe. These are delivery delays, not failures. The raw materials ordered will arrive as soon as the supply bottlenecks have been resolved.
With the current geopolitical bottlenecks, this is not necessarily the case. The production capacities of Russian and Ukrainian suppliers are unavailable for the time being. It will take years to rebuild Ukraine’s economy and infrastructure, and how long the Western industrialized countries’ sanctions against Russia will last is unclear. This is not a temporary increase in delivery times. Supply relationships have been damaged for the long term, at least until the situation eventually stabilizes.
In the short term, the current situation is the same as the previous shortage of raw materials during the pandemic. Therefore, the countermeasures are also identical: evaluate alternative materials, seek cooperation with other companies, etc. We have already described corresponding strategies in another blog post.
However, differences become apparent in the medium and long term. The war in Eastern Europe corresponds to the escalation of a political trend that has been emerging for years. More and more countries are aligning their trade and resource policies with national interests and using them as leverage in geopolitical negotiations. It cannot be ruled out that international trade relations will be affected more frequently by political disputes in the future. For companies, this means above all that they should restructure their supply chains in the long term in order to be able to secure their resource needs even in times of crisis.
Logistics center with low inventory
Firstly, it is advisable to reduce the complexity of the supply chain in order to mitigate the effect of external influencing factors (punitive tariffs, sanctions, etc.). For example, decision-makers should rethink their current just-in-time strategies and take the warehouse off the road, at least in part. Keeping critical components such as rubber compounds or precursors in stock can give rubber processing companies the time to take countermeasures in crisis situations without having to accept production losses.
It is also advisable to restructure supply chains, with a stronger focus on Central and Western European suppliers. Local partners can react more quickly in times of crisis, as their transport routes are shorter and their goods hardly have to cross borders or bottlenecks. In addition, there is less risk of trade conflicts within the EU, which could affect supply relationships.
In addition, companies should monitor geopolitical developments more closely. Conflicts and crises often take a long time to emerge, giving decision-makers the opportunity to react in good time. However, this requires precise monitoring of the political situation in the countries with which the organization maintains trade relations, as well as up-to-date information on the state of diplomatic relations and potential causes of conflict.
Diversification of the supply chain is also advisable, especially in terms of geographic distribution. It is worthwhile to have suppliers in different countries on hand in order to be able to switch to other, non-sanctioned trading partners in crisis situations. Although this goes against the trend toward supplier consolidation in the industry, it does create stability. When in doubt, companies must weigh both sides against each other.
The war in Ukraine and the sanctions against Russia have also hit the rubber processing industries hard. Numerous supply chains have been cut off and it is unclear if and when the situation will return to normal. This is exacerbating the pandemic-related shortage of raw materials and putting industrial companies in a tight spot due to rising raw material prices.
Currently, the weaknesses of complex, international supplier structures that have long characterized the manufacturing industries are becoming increasingly apparent. In this context, companies should carefully consider whether the efficiency benefits of a just-in-time strategy are worth the increasing risk of supply shortages and production downtime. This issue is something that is likely to influence global purchasing strategies more frequently in the future.
Whitepaper: Secure the Start of Production
Learn which factors influence your SOP!
Oksana Holovey studied business administration at the Lviv Business Academy in Lviv (Ukraine) with a focus on product manufacturing technology and commerce. She has been working for Jäger in the export sales field service for the Hanover location since 2019.
Share post now!
Jäger Gummi und Kunststoff GmbH
Lohweg 1
30559 Hannover
Tel. +49 511 – 53580
Fax +49 511 – 553394
info@jaeger-gk.de
Management:
Dipl.-Ing Sebastian Jäger
Julius Jäger, M.Sc.
Hanover Register Court HRB 59798
DE 813 314 161
Petra Dirlenbach