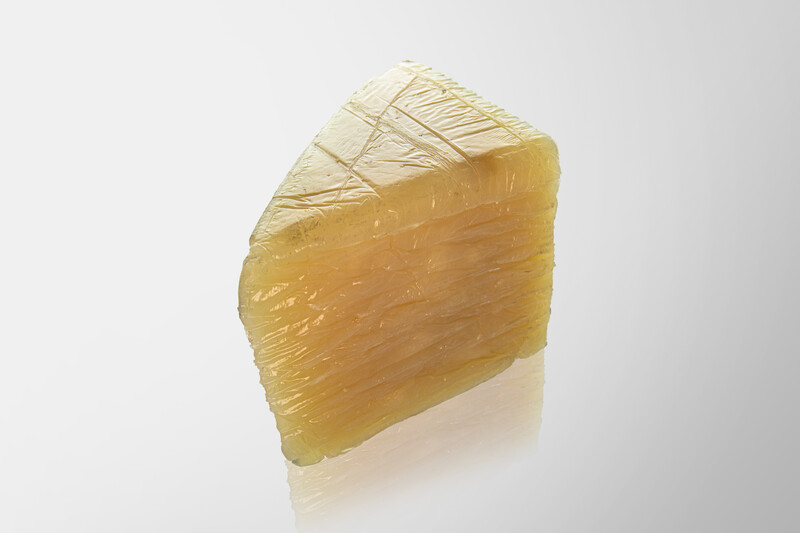
JÄGER Business Blog
WHITEPAPER
Find out which factors influence your SOP!
In many manufacturing companies, the design department is metal-centric. Rubber and plastic molded parts do not appear on their radar until all metal components are final and only a few gaps in the drawings need to be closed. The reason for this is the professional background of many designers. They mainly come from the metal sector and have little experience with plastics or elastomers. This can lead to problems, because expertise cannot always be transferred from one group of materials to another. It therefore makes sense to involve development partners in projects as early as possible to close these experience gaps.
A major difference between metallic materials and elastomers or plastics is the flexibility of their characteristics. This fact often poses challenges for designers when selecting materials.
The properties of metals are largely fixed. If you choose a particular metal for your design, you can be sure that the material will always have the same characteristics. These properties are well documented and available in the form of material lists. However, it is hardly possible to adapt the specifics of a metal to the application scenario.
Plastics and elastomers, on the other hand, are flexible. They also have basic properties, but these can be modified by adding additives. As a result, the characteristics of a rubber or plastic material depend on its configuration. For example, if you buy a particular rubber compound from two different suppliers, you will not get exactly the same product. There are always differences resulting from the additives used.
In other words, elastomers and plastics have a higher variable content in their composition than metals. Their properties always depend on the context and can be precisely adapted to the area of application. Metals, on the other hand, are fixed. Their specifics can only be changed to a small extent.
In practice, this difference is mainly noticeable in the selection of materials. When designing a metal part, the designer can choose from a wealth of materials and select the most suitable one. However, it cannot modify it further. When designing a rubber or plastic molded part, the material selection process is somewhat different. Here, the design department chooses a basic material and adapts it to the conditions with various additives. This is a change for experts who have little experience with plastics and elastomers. You can’t buy a material “out-of-the-box”; every compound is different.
Of course, there are exceptions. Especially for widely used applications, there are prefabricated rubber or plastic compounds that already have all the necessary properties. However, the design must first check whether the material is suitable for the product at hand. Every compound is different. It is therefore worth consulting experts who can point out specific differences.
Engineer on machine
Another difference between the two groups of materials concerns the manufacturing process. Items made of metal are fundamentally manufactured differently than items made of rubber or plastic. For example, pressing, injection molding and extrusion are common production techniques for molded rubber parts. In the metal sector, on the other hand, these techniques are somewhat different.
In practice, this means that experience in the production of one group of materials often cannot be transferred to another. This can have a negative impact on the design of a molded part, because there are geometries that can be easily implemented with metal but not with rubber or plastic.
For example, in the metal sector, people like to work with fine contours and pointed geometries that require very tight tolerances. Rubber, however, is a natural material that cannot be manufactured as precisely as metal. The technical framework conditions do not permit this. If, for example, the design department drafts a molded rubber part that is characterized by very filigree geometries, a high level of scrap can usually be expected. Some of the items produced do not fit into the machine or assembly, others are simply defective.
When working with rubber and plastic, the design must take into account that these materials are “alive” and therefore always have a certain minimum level of deviation. However, this requires experience with this group of materials.
Contact with a development partner for rubber and plastic molded parts is not only useful for gaining expertise in the material. The supplier can also contribute insights into the current market situation as well as design details suitable for rubber and plastics.
For example, rubber and plastics producers know which materials are currently difficult to supply or price-intensive. They can also contribute long-term forecasts, for example when science and politics are currently discussing whether certain materials should be banned for environmental or health protection reasons. In such cases, the design can specifically avoid these materials and switch to alternatives.
These advantages apply not only to production companies that have little experience with plastics and elastomers. Even for “old hands”, regular exchange with a development partner is worthwhile in order to stay up to date.
In many development projects in the manufacturing industry, rubber and plastics producers are brought on board too late. This can be detrimental to the project because experience gained in metal design cannot always be transferred to plastics or elastomers. There are subtle differences that can delay the development process if not taken into account. It therefore makes sense to involve experts who can contribute experience with these materials right from the start.
Whitepaper: Secure the Start of Production
Learn which factors influence your SOP!
Share this post!
Jäger Gummi und Kunststoff GmbH
Lohweg 1
30559 Hannover
Tel. +49 511 – 53580
Fax +49 511 – 553394
info@jaeger-gk.de
Management:
Dipl.-Ing Sebastian Jäger
Julius Jäger, M.Sc.
Hanover Register Court HRB 59798
DE 813 314 161
Petra Dirlenbach