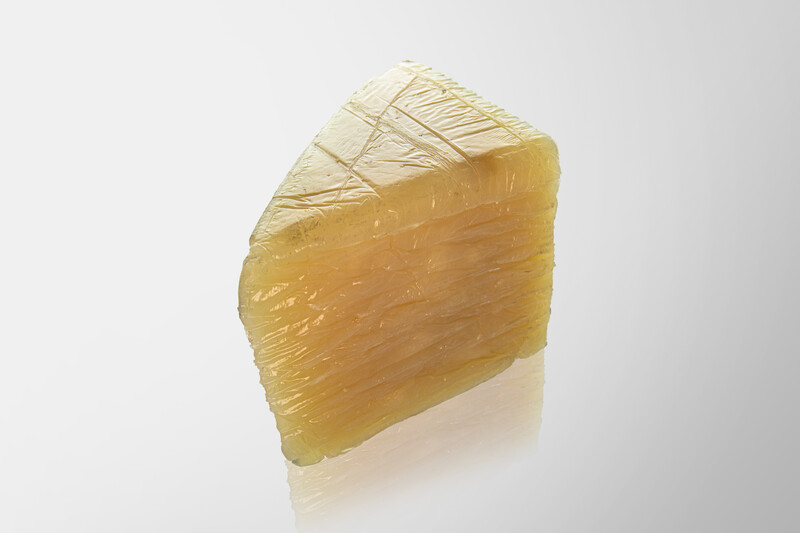
JÄGER Business Blog
WHITEPAPER
Find out which factors influence your SOP!
Materials science is constantly evolving. Every year, new materials come onto the market that are lighter, more robust and more environmentally friendly than the previous ones. So it makes sense for manufacturing companies to regularly check whether there is a better alternative for the components they use. In practice, however, this happens relatively rarely. Many decision-makers do not consider the optimization potential offered by rubber and plastic parts. In doing so, they forego a possible competitive advantage.
Manufacturing companies usually only replace components when there is a defect or the product requirements are no longer met. However, it can also be worthwhile to put installed rubber and plastic parts to the test without a specific reason, because more modern alternatives often offer a number of advantages.
The manufacturing processes for rubber and plastics are constantly evolving. In the course of this, products can be manufactured more robustly and with less material input through the targeted adaptation of materials. For example, a rubber hose seal needs to be less thick because it does not crack as quickly and has less wear and tear. It also happens that companies have selected an expensive material that significantly exceeds product requirements. In view of rising raw material prices, it may be worthwhile in such a case to switch to a less expensive material with similar properties
Products made of more up-to-date materials have a longer service life and therefore require less frequent maintenance or replacement, which reduces the burden on service. Their technical assembly is also easier. For example, parts that are mounted overhead may include an adhesive film that allows temporary attachment during locking. Alternatively, the company can purchase its rubber or plastic components directly as finished assemblies from its production partner.
Another important point is the issue of sustainability. Newer components are often more environmentally friendly because they contain fewer pollutants and are even biodegradable in some cases. They also have less of an impact on the environment during production, as their manufacture requires less energy and material input. This is a major advantage for companies that face strict legal requirements in their industry, want to improve their image, or generally want to become greener.
Materials that contain substances that are harmful to the environment or health are repeatedly the focus of the regulatory authorities. If they are banned or the manufacturer withdraws them from the market for other reasons, there is no longer any supply available for some components. In this case, it makes sense for manufacturing companies to rework these parts and switch to future-proof materials.
If a company decides to modernize a rubber or plastic component, there are basically two starting points: the manufacturing process and the product configuration.
During the production of a rubber or plastic product, there is always material loss. If the part is milled or turned, material is lost in the form of chips or cutting waste. In injection molding, the loss is less, but even here some material always remains as sprue.
This waste is particularly relevant in rubber production, since the vulcanization process is irreversible and material waste cannot be returned to production. Such material losses can be reduced by a more efficient mold and production concept.
Furthermore, it is possible to reduce cycle times by adjusting the product configuration. The more solid or thick-walled a production part is, the longer heating or cooling takes. However, if the part is designed so that the walls are thinner, these times are reduced and production is accelerated. At the same time, energy consumption and material usage are reduced, making the component cheaper and more environmentally friendly.
At first glance, the optimization of the manufacturing process seems to be the responsibility of the production partner. However, the specification of the rubber or plastic component usually comes from the customer. If the customer designs a part in such a way that it can be manufactured more easily, he also benefits from shorter delivery times and lower costs.
Older rubber and plastic parts in particular often consist of materials that are no longer state of the art. Putting them to the test and redesigning them is usually worthwhile. A simple change in material can make a component lighter, more robust and less sensitive. Reworking the geometry can also be worthwhile, often in conjunction with a different material. For example, if a more robust material is used, the outer walls of a component can be made thinner while maintaining the same level of resistance. This reduces both material and energy consumption.
Even with more modern components, it can be worth considering a change of material, especially for expensive materials. Sometimes designers use brand names synonymously with the material designation and thus unintentionally install premium parts, even though the customer has not explicitly requested this. In such a case, it is often advisable to switch to a cheaper alternative that more accurately meets the real requirements.
Modernization measures in manufacturing companies are usually limited to processes and infrastructure. Only a few decision-makers have the installed components on their radar. Yet it can be worthwhile to regularly put rubber and plastic parts to the test and see if a better solution can be found. Alternative materials as well as more modern tooling concepts and manufacturing processes ensure that components are becoming ever more affordable, robust, efficient and environmentally friendly. Those who update them at regular intervals can often realize competitive advantages.
Whitepaper: Secure the Start of Production
Learn which factors influence your SOP!
Thomas Dyckrup has been with Jäger since 2007. The qualified wholesale & foreign trade merchant has been head of the Oldenburg site since 2019, following positions in internal sales and key account management.
Share this post!
Jäger Gummi und Kunststoff GmbH
Lohweg 1
30559 Hannover
Tel. +49 511 – 53580
Fax +49 511 – 553394
info@jaeger-gk.de
Management:
Dipl.-Ing Sebastian Jäger
Julius Jäger, M.Sc.
Hanover Register Court HRB 59798
DE 813 314 161
Petra Dirlenbach