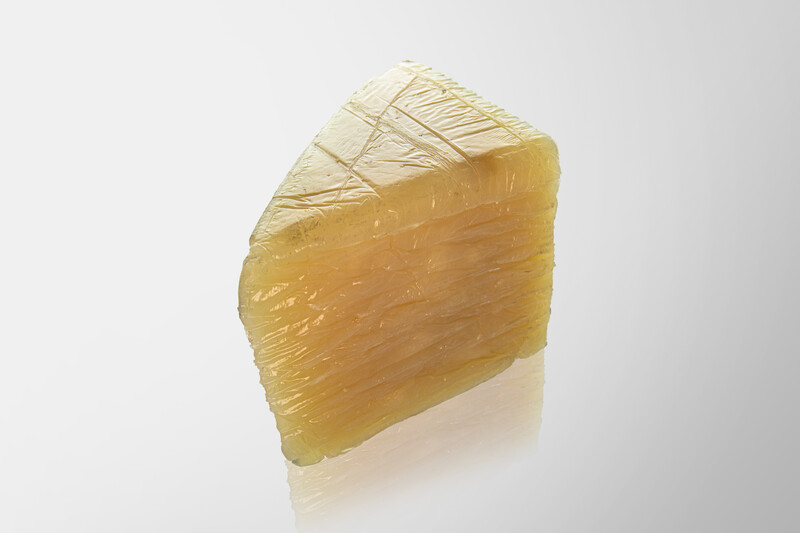
JÄGER Business Blog
How to make your resource procurement crisis-proof
WHITEPAPER
Find out which factors influence your SOP!
The current shortage of raw materials has bumped many manufacturing companies off. There has never been a comparable crisis before, so hardly any organization was prepared for it. However, sticking your head in the sand will not help. Procurement experts should regard the current situation as a wake-up call and increase their supply security for the future. The following six tips for more crisis-proof resource procurement will help you to do this.
In some manufacturing companies, design is constrained in material selection. It has only a small number of approved materials available, which are often very specific. In most cases, these are specific items from individual manufacturers with individual product codes. This approach is normally very efficient because it minimizes the necessary approval processes. Once the materials have been approved, the design department can install them again and again without having to consult them. In addition, procurement can realize economies of scale by purchasing larger quantities of specific products.
In times of crisis, however, this lack of flexibility becomes a serious disadvantage. If an approved material is not available, the design department cannot simply switch to an equivalent. Instead, it has to apply for a new release, which leads to delays.
To avoid this problem, give your designers as much leeway as possible in material selection. Be as general as possible and as specific as necessary. Do not rule out options that you can fall back on in the event of a crisis.
A lean supplier network certainly has advantages. It’s easy to maintain and enables closer relationships with suppliers, which translates into greater transparency and advantages in price negotiations. However, it also carries risks, especially in extreme cases.
For example, if a company has only one supplier for each material, it creates a number of single points of failure. If the supplier cannot deliver, the supply of materials comes to a standstill. The result is delays in production.
It is better to ensure that you have redundancies in your supplier network. For each material, you should have at least one second-source supplier on hand so that you can switch in an emergency. Alternatively, you can select suppliers who have a robust supplier network themselves and can call in a partner in the event of supply difficulties.
Information about expected material requirements is an important prerequisite for robust resource procurement. The more transparent you make your sales planning, the easier it will be for them to order appropriate quantities from your suppliers.
Also keep in mind that your suppliers are part of a larger supply chain and will need to procure resources themselves to service your orders. If you order as early as possible and formulate your specifications precisely, you can significantly reduce the risk of disruptions or errors.
You gain transparency regarding resource requirements by strengthening your forecast. Create the necessary processes early on and invest in software and personnel. This will make life easier for you and your suppliers.
Teammeeting
In the context of globalization, it is common practice in most industries to procure resources primarily from international suppliers. The reason for this procurement strategy is the price advantage that suppliers from low-wage countries have over local competitors. But price is not everything. Transporting goods and raw materials halfway around the world carries a high risk of disruption, because of the distance traveled. Shipments pass through numerous transshipment points and chokepoints on their way from Southeast Asia to Europe, all of which offer some potential for delays. An example of this is the Suez Canal blockade in March 2021, which impacted a significant portion of the global movement of goods.
Instead of meeting all of your resource needs through global suppliers, consider adding more local suppliers to your network. These feature short transportation and communication paths, so there is less potential for disruption and problems can be sorted out more quickly.
Procurement is not an isolated process that applies only to your own company. Every organization is part of a supply chain that extends from the extraction of raw materials to the production of goods. Any disruption along this chain also impacts subsequent steps in the value creation process. Therefore, a robust procurement strategy should always include suppliers and upstream suppliers.
This requires a solid information base. You should know where your suppliers obtain resources from and how their procurement processes are structured. To this end, it is advisable to create a well-maintained supplier database that contains all the important information. A database like this gives you the opportunity to perform a complete risk analysis that includes your entire supply chain.
As part of the just-in-time approach, many manufacturing companies have moved to reduce their inventory levels and instead rely on demand-synchronized deliveries of goods. This strategy is highly efficient because it makes traditional warehousing largely obsolete. However, it is also highly vulnerable to disruptive events. If a disruption or delay occurs in procurement, it has an immediate impact on production processes because there are no relevant safety buffers.
As a preventive countermeasure, it is advisable to rethink inventory strategies and place more emphasis on a stable supply of resources. Increase your safety stocks so that your production can temporarily compensate for supply shortfalls. Adjusting lot sizes is also advisable. Refrain from ordering demand-based material quantities at short intervals. This strategy is too prone to disruption. If possible, place larger orders and stockpile some of the material.
Whitepaper: Secure the Start of Production
Learn which factors influence your SOP!
The measures presented seem counterintuitive at first. After all, they run counter to common supply chain management best practices: price orientation, minimizing inventory costs, just-in-time delivery, etc. However, keep in mind that these best practices are the result of an ongoing optimization process that has gone on for decades without major disruption. Today’s supply chain management is designed to operate as efficiently as possible under optimal conditions. However, when serious disruptions occur, the resilience to respond appropriately is lacking.
The Corona pandemic demonstrated the importance of robust sourcing strategies. It is likely that similar crises may occur in the future. In view of this, it is worth accepting minor efficiency losses in supply chain management in order to significantly increase resilience in return.
Hannes Bolting has been working in sales at Jäger since 2018. At the same time, the trained industrial clerk is completing a master’s degree with a focus on sales management at the FOM Hochschule für Ökonomie & Management in Hanover.
Share this post!
Jäger Gummi und Kunststoff GmbH
Lohweg 1
30559 Hannover
Tel. +49 511 – 53580
Fax +49 511 – 553394
info@jaeger-gk.de
Management:
Dipl.-Ing Sebastian Jäger
Julius Jäger, M.Sc.
Hanover Register Court HRB 59798
DE 813 314 161
Petra Dirlenbach