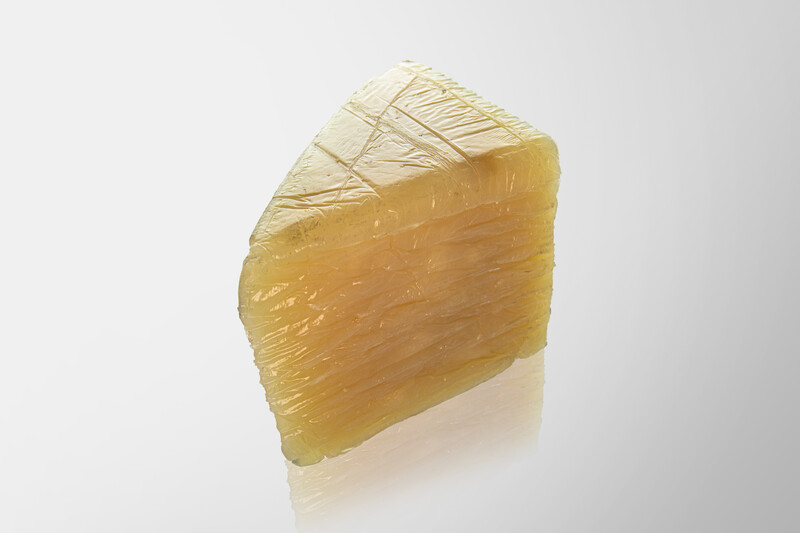
JÄGER Business Blog
plastic also deserve attention
WHITEPAPER
Find out which factors influence your SOP!
Although C-parts account for up to 80 percent of a product, they lead a shadowy existence in design. Designers tend to focus their attention on high-priced A parts. C-parts, on the other hand, are often only dealt with by the purchasing department. This approach is understandable. But neglecting C-parts can lead to problems in the long term, especially in the rubber and plastics sector.
C-parts are among the hygiene factors in most companies. As long as they fulfill their functions and do not cause any problems, their handling is reduced to procurement. They are rarely the target of optimization measures. Instead, C-parts made of rubber or plastic often only receive attention in design when the equipment designs have been completed. As a rule, designers simply select a standard part whose product description superficially meets the requirements. Additional measures, for example complex analyses or validations, which are standard for A-parts, only take place rudimentarily, if at all. The reason for this is simple: Compared to A and B parts, the optimization of C parts has a low cost-benefit ratio. C-parts are cheap and hardly contribute to the core properties of a product. Optimizing them costs time, but this is hardly reflected in the end result. What advantages would it have for a company to jeopardize the Start of Production (SOP) for such marginal effects?
C-parts are components that account for a disproportionate share of a product's total volume but only marginally affect its value. According to Pareto, C-parts account for 80 percent of the volume but only 20 percent of the value. Examples of C-parts are seals, O-rings or plastic caps.
However, the niche existence that C-parts made of rubber or plastic lead does not only affect the design. They also enjoy only low priority in the ongoing production process. If it becomes necessary to replace a C-part (for example, due to delivery problems on the part of the supplier), the new part is usually not tested again for suitability. Those responsible simply select an alternative component that, according to the manufacturer’s specifications, has comparable properties. The fact that a new component may, in the worst case, not be fully compatible with the specifications is often accepted in view of the threat of delay.
In addition, C-parts in industry are often selected based on price. Given the small contribution to the core properties of the finished products, the design department likes to choose inexpensive materials to reduce overall costs. In places, companies also lack the expertise to give rubber or plastic C-parts the attention they deserve. They underestimate the complexity behind such components and instead focus on cost. The result is that high-priced A and B parts are supplemented in production by cheap goods that pose a risk of damage to the overall system.
This is not a criticism of purchasing or construction. The colleagues merely act according to the specifications and incentives they receive. C-parts are simply not given enough importance in typical production companies. However, this can lead to problems occurring or potentials remaining unused.
Plastic cover caps in various designs and O-rings
From a financial point of view, C-parts may have little relevance. Nevertheless, they are an essential part of any machine or system. Damage to a C-part can have serious consequences for the entire system, even leading to its failure.
Consider, for example, a feed pump in a chemical industrial plant, a case that concerned Jäger a few years ago. The customer had chosen a shaft seal to seal the pump – a low-cost option, but one that had insufficient chemical resistance. After some time, the seal became porous and chemical solutions leaked out. The plant had to be temporarily shut down, and replacing the pump and restarting it resulted in lost production and high costs. A suitable shaft seal would have been more expensive than the cheap version, but would have avoided the subsequent costs of system damage.
Unfortunately, those responsible had not paid the necessary attention to the seal, a C-part. They opted for the cheaper part and accepted the shorter service life of the component.
Another example: dampers are rubber-metal elements whose materials are joined by a chemical bonding agent. If the bonding agent is incorrectly chosen (for financial reasons, for example), the damping can fail after a relatively short time, exposing the machine to harmful vibrations. The financial advantages are thus negated by a shorter service life of the products.
When dealing with C-parts, most manufacturing companies focus on procurement costs and processes, not on optimization. Many producers install C-parts as standard that have not been modernized for years.
But materials science is constantly evolving. New elastomers and plastics are constantly coming onto the market that are lighter, more resistant, more environmentally friendly or cheaper than previous materials. Replacing an obsolete C-part can have a positive impact on the characteristics of the finished products, outweighing the cost of upgrading despite the low value of the material.
In some cases, it turns out that a C-part is obsolete and no longer meets the requirements of its intended use. This problem can occur when a machine or system is further developed without adapting the installed C-parts. These are then designed for conditions that no longer correspond to the current status.
As a result, the product properties are negatively affected, for example by a seal that becomes brittle more quickly because it comes into contact with media for which it was not designed. In the worst case, there is even a higher risk of product failure.
In the rubber and plastics sector, it is tempting to save on the components that make the smallest contribution to the monetary value of a product. However, neglecting C-parts can have negative consequences. Not only does the risk of failure of the overall system increase due to a shorter service life of some components. The organization also leaves optimization potential lying fallow that could significantly improve the properties (and thus the performance) of the end product.
Companies should therefore not save at the wrong end. It is worthwhile not only reducing C-parts made of rubber or plastic to their procurement cost, but also making them a stronger focus of the design.
Whitepaper: Secure the Start of Production
Learn which factors influence your SOP!
Thomas Wutke has been managing the Jäger site in Frankfurt am Main since 2020 and was previously responsible for another site. He has more than 35 years of experience in sales (KAM/B2B) of rubber and plastics as well as in project management and application development.
Share post now!
Jäger Gummi und Kunststoff GmbH
Lohweg 1
30559 Hannover
Tel. +49 511 – 53580
Fax +49 511 – 553394
info@jaeger-gk.de
Management:
Dipl.-Ing Sebastian Jäger
Julius Jäger, M.Sc.
Hanover Register Court HRB 59798
DE 813 314 161
Petra Dirlenbach