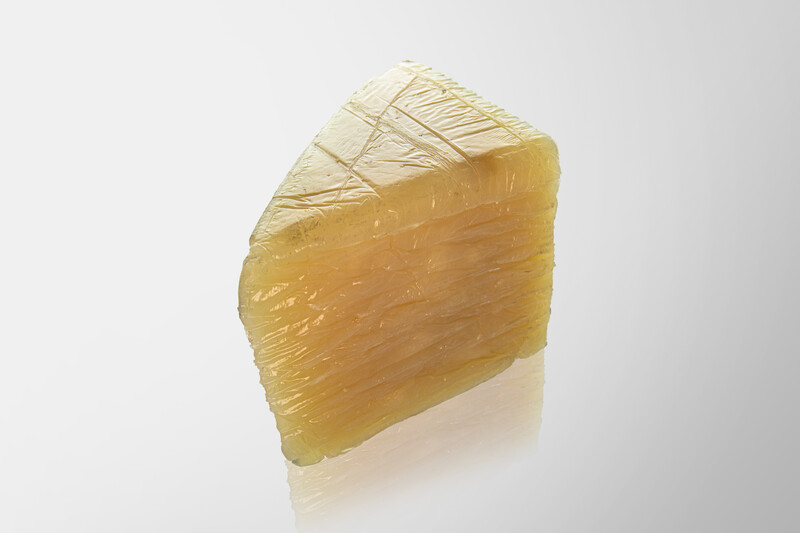
JÄGER Business Blog
when it comes to hose assemblies.
WHITEPAPER
Find out which factors influence your SOP!
Along with pipes, hoses are the means of choice when it comes to transporting liquids, solids or gases. However, hardly any production companies think about this topic. However, there are a number of potentials for optimization and sources of error in the handling of hose lines that decision-makers should be aware of.
Here are five things to consider.
As with other plastic and elastomer products, the application of a hose design is critical. There is a suitable hose for every situation. If, on the other hand, companies choose the wrong product or material, they risk losing efficiency or increasing maintenance costs – and, in the worst case, risking injury.
In general, there are four important questions that manufacturing companies must answer when choosing a hose design:
The pressure affects the stresses to which the hose construction is subjected on a daily basis. The higher the pressure, the more robust the hose must be. Especially since constructions that are under high pressure always involve risks of injury.
The medium to be transported primarily influences the choice of material. On the one hand, companies should ensure that the hose does not become cracked or brittle under the influence of the medium. This can happen, for example, with fuels, acids or abrasive materials such as gravel or sand. The hose material should therefore have appropriate resistance. On the other hand, it is particularly important in the food or drinking water sector that the hose line does not contaminate the medium. Here, companies should make sure that the hose has the usual certifications in their industry.
The operating temperatures also have an impact on the service life of a hose design. Temperature extremes or strong fluctuations in particular can cause a hose to quickly become brittle. The most important factors here are the temperature of the medium to be transported and the ambient temperatures of the machine or system in which the hose is installed.
In addition, there are environment-specific operating conditions that can have a stressing effect on a hose construction. These include UV radiation and ozone exposure, weathering, and static or mechanical loads.
The properties of a hose construction depend not only on the elastomeric components, but also on the fittings. Companies sometimes underestimate this fact. They make sure that the hose meets all the application criteria, but overlook the metal components. This can affect the entire design.
For example, the fittings must have the same resistance to acids, fuels or abrasive materials as the elastomer components, since they are exposed to identical media. It is also important to look for materials to which rubber is natively resistant, but metal components are not necessarily (for example, water).
Hose assemblies in red and blue
Particularly in the food and drinking water sectors, companies should make sure that all components of the hose design have the industry-standard certifications. Otherwise, there is a risk that the design will become unusable for the application scenario, for example, if food is contaminated by metals that are harmful to health.
In an industrial context, hose assemblies often carry hazardous substances. Therefore, safety aspects have a high priority. Incorrect handling of hoses not only threatens machine breakdowns, but also the risk of injury.
High-pressure hoses, for example, can burst or tear out of fittings and injure bystanders by whipping. Even small cracks or holes pose risks, as fluids can escape at high pressure and inject harmful substances into the skin.
Companies can minimize these risks by choosing a suitable elastomer. It is also important to assemble the hose design correctly, for example by observing bending radii or avoiding torsion. When in doubt, it is advisable to use fittings that are resistant to tear-out.
Installation situation hose line
Special attention should be paid to areas of application where there is a risk of explosion. Here, there is a risk of the hose construction becoming electrostatically charged and a spark igniting the volatile gas-air mixture. The same applies to areas where there is a risk of dust explosions (for example, when processing flour or sawdust). If the hose construction is to be used in an EX zone, it must therefore be electrically conductive and grounded. All components of the construction should have ATEX certification, both the hose and the fittings.
When customers contact an elastomeric products supplier for a hose design, their specifications are often not designed with practicality. In some cases, their design drawings provide for configurations that cannot be implemented in this form. Examples include bend radii that are too small, minimum lengths that are not met, or a lack of freedom of movement for the hose, which leads to abrasion. Design errors of this kind usually result in a reduced service life of the hose construction.
For this reason, it makes sense to seek early contact with material experts who have experience with hoses and can provide their expertise. It is always easier to adapt a product, machine or system during the planning phase. On the other hand, once pre-production has started, the cost of a change increases significantly.
When selecting a hose design (as in the plastics and elastomer sector in general), two extremes can often be observed. On the one hand, companies like to focus on price and always go for the cheapest option. On the other hand, some decision-makers often think “a lot helps a lot” and go for premium products. Both approaches are counterproductive.
Inexpensive hoses realize their low price partly at the expense of quality. They have a shorter service life and have to be replaced more frequently. The rising maintenance costs quickly put the purchase price into perspective, making the hose more expensive in the long run.
Even premium products are not always the best choice. Often, companies rely on hose assemblies that far exceed their requirements, which is reflected in the cost. At the same time, the better features don’t necessarily provide real added value. For example, a hose that can withstand 15 bar has no advantage over a hose that can withstand 10 bar if the company only wants to pump materials through it at 8 bar.
There is a hose for every application. The best way is to choose a product that meets the specific requirements, but doesn’t go too far beyond that.
Unfortunately, there is no such thing as universally applicable hose assemblies. Which product should be used always depends on the context. Every company has individual requirements for a hose design that include financial, technical, process-related or safety aspects. It is therefore worth giving the topic the attention it deserves.
Whitepaper: Secure the Start of Production
Learn which factors influence your SOP!
Share this post!
Jäger Gummi und Kunststoff GmbH
Lohweg 1
30559 Hannover
Tel. +49 511 – 53580
Fax +49 511 – 553394
info@jaeger-gk.de
Management:
Dipl.-Ing Sebastian Jäger
Julius Jäger, M.Sc.
Hanover Register Court HRB 59798
DE 813 314 161
Petra Dirlenbach