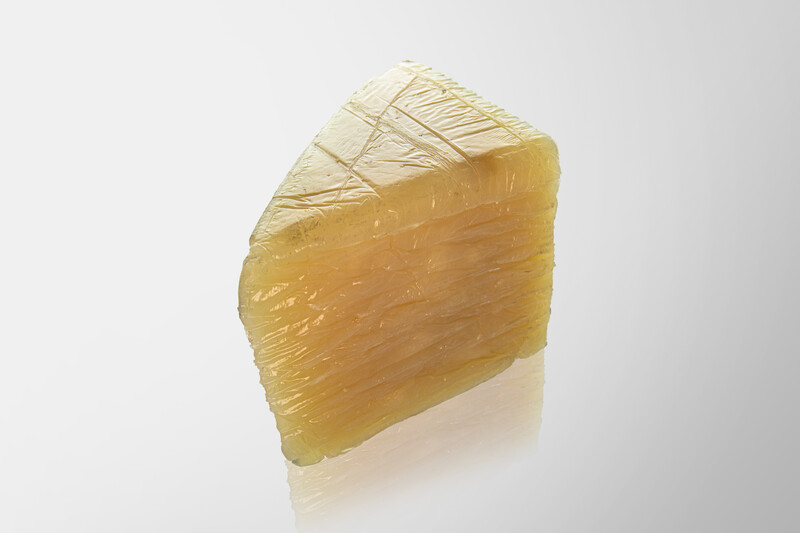
JÄGER Business Blog
WHITEPAPER
Find out which factors influence your SOP!
Rubber and plastic have become indispensable in medical technology. Thanks to their flexible properties, they are ideal for use in doctors’ offices, hospitals and care facilities. They are unbreakable, easy to clean, do not absorb odors and have a low allergy risk. However, the development of medical rubber and plastic solutions is challenging because they are subject to strict regulations and high quality requirements.
The properties of plastics and elastomers can be flexibly adapted to the area of application by adding additives. Depending on their composition, their characteristics are stronger or weaker. This makes them attractive for the medical sector, which is characterized by high requirements. A material that can be flexibly tailored to a specific sterilization process, for example, is of great value here.
At the same time, it should be noted that single-use products are frequently used in medicine, which are supplied sterilized and disposed of after use. Price therefore plays a major role. Disposable syringes, for example, which are ordered by the thousands by hospitals, must not have high unit costs.
Nevertheless, the quality requirements of the medical industry still apply. To achieve this balancing act, flexible materials are needed whose characteristics can be precisely modified.
There are many areas of application for elastomers and plastics in medical technology. Examples include:
In addition, the materials are used in electronic components installed in medical devices. For example:
Disposable gloves and syringes as an application area for polymers
Medical technology places high demands on rubber and plastic products, because defects can have serious consequences for the health and life of patients. The specific requirements depend on whether and how the product comes into contact with the body.
All medical devices that come into direct contact with patients are required to be biocompatible. This means that they must not have any negative effects on the organism and must be free of harmful substances or side effects. The exact specifications of biocompatibility are defined in ISO 10993.
It should be noted that biocompatibility can also affect peripheral devices, in the form of indirect relationships. This is the case, for example, with plastic bags for blood products. Although the bag itself does not come into contact with the human body, its contents do. The plastic must not contaminate the blood bag. So here, too, biocompatibility is an absolute must.
Medical technology is characterized by a wide range of requirements. Here, plastics and elastomers are exposed to various chemicals, cleaning agents and solvents and must meet high quality standards. All these factors have a direct influence on material selection.
The sterilization process in particular presents medical device manufacturers with challenges, as it exposes the material to unusual stresses. Depending on the type of sterilization, medical equipment must withstand high temperatures, radiation or contact with certain gases without changing its characteristics. These additional requirements must be considered in material selection and limit options.
Among others, the following factors influence material selection in medical technology:
Various materials for medical technology
Silicone is a biocompatible high-performance rubber that is characterized by its outstanding resistance to aging, weathering and temperature. It is insensitive to alcohol and can withstand temperatures up to 250 to 300 °C (depending on the compound), so it can be easily sterilized. Thanks to its resistance, silicone is often used for functional components that must not fail.
EPDM is a tough, durable synthetic rubber used in various medical products. It is insensitive to water (steam), alcohol, acids as well as alkaline solvents. Cleaning and sterilization are therefore no problem. In its basic form, the material is not biocompatible. However, this property can be achieved by additives. EPDM is very resistant and therefore an excellent all-round material for medical technology.
Polyethylene (PE), the most widely used plastic in the world, has several characteristics that make it attractive to the medical industry. It is resistant to acids and alkalis, biocompatible, wear-resistant and relatively inexpensive. PE is used for packaging and syringes.
Polypropylene (PP) is similar to polyethylene in terms of distribution as well as chemical and mechanical properties. The material is robust, resistant to cleaning agents and disinfectants and withstands high temperatures. PP is often used for packaging, housings and syringes.
Polystyrene (PS) is particularly interesting for the medical industry because of its optical properties. The material has a high transparency and is therefore well suited as a glass substitute. Among other things, PS is used for bottles, measuring beakers and Petri dishes.
PVC is a robust, durable material that is very easy to process and extremely inexpensive. In medical technology, it is used for hoses, catheters and disposable gloves, among other things. Since PVC is very hard, plasticizers are often added to the material, which in the past caused health concerns. In the meantime, however, these additives are DEHP-free (di(2-ethylhexyl) phthalate) and therefore very suitable for medical use.
Plastics and elastomers have become standard materials in medical technology. They are lightweight, robust, harmless to health and relatively inexpensive. In addition, their material properties can be flexibly adapted to the area of application. However, it is important to carefully specify the product requirements. Particularly in the medical industry, it can be difficult to find a material that optimally meets all specifications, given the high quality requirements. If in doubt, it is therefore advisable to consult material experts who are familiar with the pitfalls of the industry.
Whitepaper: Secure the Start of Production
Learn which factors influence your SOP!
Tobias Bettels is a sales representative at Jäger. The state-certified business economist has more than 20 years of experience in plastics sales and worked in medical technology for eight years.
Share this post!
Jäger Gummi und Kunststoff GmbH
Lohweg 1
30559 Hannover
Tel. +49 511 – 53580
Fax +49 511 – 553394
info@jaeger-gk.de
Management:
Dipl.-Ing Sebastian Jäger
Julius Jäger, M.Sc.
Hanover Register Court HRB 59798
DE 813 314 161
Petra Dirlenbach