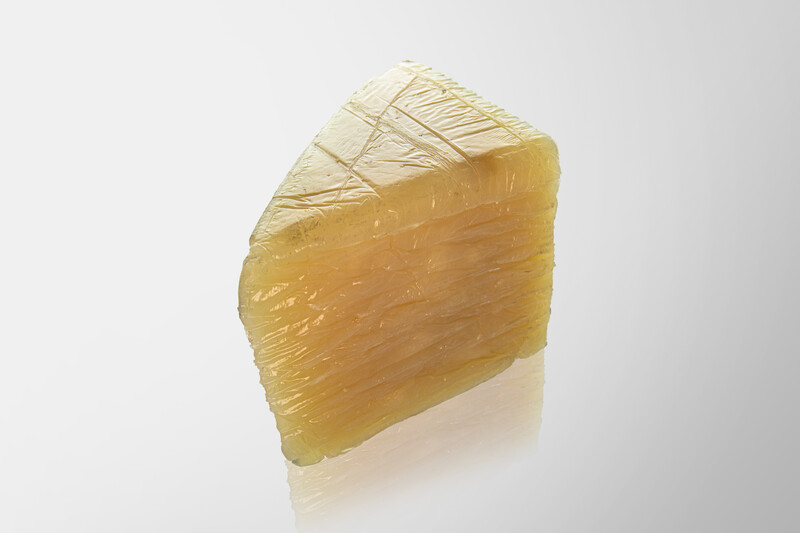
JÄGER Business Blog
WHITEPAPER
Find out which factors influence your SOP!
Injection molding processes are ideal for high-volume production of plastic components. Once the mold has paid for itself, the unit costs are relatively low. However, this production technique is often unprofitable for small batches, as mold construction often represents a disproportionate share of the manufacturing costs for small quantities. Fiber composites, which are usually manufactured by vacuum infusion, offer an alternative for large-area parts.
Injection molding and vacuum infusion processes are based on different principles. In injection molding, the liquid material is pressed into the mold under high pressure, while vacuum infusion sucks the material in by negative pressure.
In practice, a laminate mold, which determines the subsequent shape of the component, is first coated with a layer of gelcoat. Precisely cut fiber mats are then inserted into the contours of the mold, forming the core of the composite. The composition of these mats depends on the application. Most common are glass and carbon fibers, but aramid fibers (e.g. Kevlar) or various mineral (basalt) or vegetable (jute, flax, cotton) fibers can also be used. For infusion, infusion tubes are placed at predefined locations and the mold is sealed all around with a film.
As soon as the preparation is complete, the air is sucked out from under the foil so that a vacuum is created. Liquid resin is now fed into the mold via the hoses, which is “pulled” into all corners and free spaces by the vacuum. The compound is therefore not actively pressed into the mold, but is pushed into the evacuated mold by the ambient pressure. To ensure that no dry spots remain, a little more resin is pumped in than necessary. The excess material is collected and recycled if possible. The resin mixture then cures under vacuum and combines with the fiber mats to form a fiber-reinforced material.
The following figure illustrates the principle. At the top, the resin is introduced into the laminate through the two feed lines. It slowly migrates through the component in a so-called flow front (boundary between dark and light yellow), while at the bottom the white suction line continues to maintain the vacuum. Finally, the flow front reaches the suction line and the filling process comes to a halt.
Example of vacuum infusion
Components made of fiber composites are often significantly lighter than injection-molded plastic components for the same performance, because the fibers give the material extreme strength in the longitudinal direction and thus indirectly reduce component weight, since less mass is required for the same load-bearing capacity. This property makes fiber composites attractive for all areas of application in which weight reduction plays a role, e.g. motor sports, boat building or aerospace.
A special feature of fiber composites is that their stiffness and tensile strength depend on the orientation of the fibers within the composite matrix. This allows their mechanical properties to be flexibly tailored to the area of application. This pays off both in terms of price and weight, as the components can be optimized specifically along the stress curves in use.
For example, fiber-reinforced composites make it possible to develop lighter tension rods that are enormously stable against loads in the direction of tension, but less able to withstand orthogonal forces (which occur less frequently).
The disadvantage of fiber-reinforced plastics becomes apparent toward the end of their service life. Unlike injection-molded parts, fiber-reinforced parts are not readily recyclable. The reason for this is the chemical composition of the material. It is not a homogeneous mass, but a compound of polymers (often duromers) and reinforcing fibers that stick together. This bond is almost impossible to reverse in terms of process technology. Components manufactured in this way can therefore not simply be melted down and recycled.
On the one hand, this is detrimental to the company’s environmental balance sheet, since fiber composites are not biodegradable and require costly disposal. On the other hand, it is detrimental to profitability, as the company has to arrange and finance disposal – a challenge that is currently occupying the operators of offshore wind farms, for example. For this reason, fiber composites are critical for application areas with a short service life.
Vacuum infusion of a rotor blade in detail
Some of the advantages and disadvantages of fiber-reinforced plastics arise not from the material properties, but from the manufacturing process. Since vacuum infusion does not require high-pressure resistant molds, the investment costs are significantly lower, which is particularly noticeable for small quantities. This circumstance makes fiber composites particularly attractive for small batches, where the high costs of toolmaking often cannot be spread over high volumes.
In addition, vacuum infusion is more suitable for large-area components, since laminate molds can be produced with less effort. For example, producing a meter-long boat hull by injection molding would be neither economical nor practical. Lining a corresponding mold manually, on the other hand, is feasible with significantly less effort.
However, the high number of manual steps is also a weakness of vacuum infusion when it comes to large series. The time required scales very poorly. As soon as larger quantities of a component are required, this manufacturing process loses its economic efficiency. Therefore, vacuum infusion is particularly suitable for small batches or individual projects.
Vacuum infusion is a common process for the production of fiber composite components. It is particularly suitable for small series or manufactures, since the investment costs for molds and tools are comparatively low and the properties of the material can be individually tailored to the application. Even very large-area components are no problem.
However, this manufacturing approach is less suitable for large-scale production because it involves a high number of manual work steps. The automation potential is therefore limited and scales poorly for large series.
For small batches, however, vacuum infusion is very well suited. The process should always be considered for corresponding projects.
We have several specialists for fiber composites in our partner network and have also already completed some projects. Contact us if you have a need!
Whitepaper: Secure the Start of Production
Learn which factors influence your SOP!
Aaron Stoffers studied dual mechanical engineering at Hanover University of Applied Sciences and Arts and later completed a master’s degree in business administration. Since 2019, he has been working for Jaeger Mare Solutions as a project manager in the field of offshore wind energy.
Share this post!
Jäger Gummi und Kunststoff GmbH
Lohweg 1
30559 Hannover
Tel. +49 511 – 53580
Fax +49 511 – 553394
info@jaeger-gk.de
Management:
Dipl.-Ing Sebastian Jäger
Julius Jäger, M.Sc.
Hanover Register Court HRB 59798
DE 813 314 161
Petra Dirlenbach