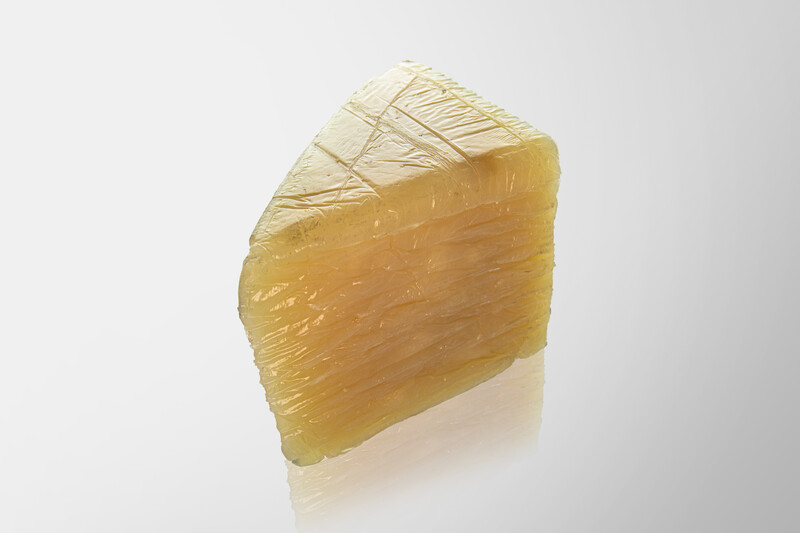
JÄGER Business Blog
profiles by roll forming
WHITEPAPER
Find out which factors influence your SOP!
Assembling edge protection profiles is time-consuming, error-prone and, in some cases, physically demanding. For this reason, it makes sense for companies to support the assembly process with technical aids. This can be achieved, for example, with roll-forming devices that work according to the roll-forming principle.
While U-shaped gasket profile is fitted with closed sides during manual assembly, these sides initially remain open during roll forming. The profile sits loosely on the edge and is only fixed in place in a second work step. For this purpose, a metal band is incorporated into the sides, which holds the seal in place after it has been pressed together.
For the fixation, a device is used which is equipped with two vertical rollers that press on the gasket from both sides. Meanwhile, a horizontal roller presses on the profile from above and holds it in place. The rollers rotate in opposite directions, causing the tool to travel along the edge and evenly press the legs together. The tool is designed for hand use. The employee only have to guide it.
The force required for this operation is low. The tool does have a perceptible dead weight, but this can be compensated for with strain relief. As a rule, the tool is operated by a pneumatic motor. However, for higher mobility requirements, the use of a rechargeable battery is also conceivable.
The biggest advantage of seal assembly via roll forming is the time saved. Putting on edge protection profiles manually is always a fiddly job, especially when there are defects or unevennesses to be removed. With the rollforming method, the fitters only have to loosely attach the profile and then run the tool over the edge. This takes much less time, which is particularly relevant for series production.
Assembly with equipment support also offers qualitative advantages. It results in a more uniform contact edge compared to the manual procedure. This is associated with force, often using aids such as hammers. The result is a wavy profile with indentations where the hammer struck. This impairs sealing performance, as the edge no longer closes completely and gaps are created.
Roll forming, on the other hand, results in a uniform sealing profile. In addition, the pull-off force is higher than with manually struck profiles, even with different flange jumps caused by sheet metal or cladding parts.
Last but not least, equipment-assisted assembly is good for the health of the employees. Mounting a profile requires force and is a strain on one side. With dozens of such operations per day, there is a risk of long-term musculoskeletal disorders. In fact, tendinitis is a common clinical picture in assembly. When used correctly, rollforming equipment relieves the strain on employees, reduces the risk of injury and thus prevents staff absences.
The equipment-supported assembly of edge protection profiles is not suitable for all areas of application. For example, tight radii (smaller than R25) and corner profiles are problematic because the device cannot go around them.
Certain profile types are also not compatible with the tool. This applies, for example, to seals with solid rubber profiles, as these absorb some of the pressure exerted by the rollers. As a result, the legs are no longer sufficiently compressed and the gasket sits too loosely on the edge, compromising sealing performance.
In order to optimally match the roll forming tool, a number of factors must be taken into account, including profile cross-section, flange thickness, radii, height jumps, cladding parts if applicable, and the location of use. If in doubt, it is advisable to consult experts who already have experience with the method.
Another disadvantage concerns the financial side. Rollforming equipment involves investment costs that must first be amortized. Therefore, this method is less suitable for companies that assemble edge profiles only in small quantities.
However, this disadvantage must be viewed in relative terms. In terms of time savings, a rollforming unit may not be worthwhile for small quantities. However, if the health of the employees is taken into account, the use of these tools is well worthwhile, even with a longer payback period.
Supporting the assembly of edge protection profiles with roll forming equipment has a number of advantages. The time required is reduced, errors occur less frequently, and the colleagues responsible are physically relieved, which prevents staff absences. It is true that these devices are not suitable for all areas of application and are associated with certain investment costs. However, these costs are amortized with the appropriate number of units. In addition, the health of the workforce is worth the financial outlay.
Whitepaper: Secure the Start of Production
Learn which factors influence your SOP!
Sascha Winter is an expert for product and process development at Jäger. The trained mold maker and technician originally comes from the automotive sector and has been working with rubber and plastics for more than 30 years.
Share this post!
Jäger Gummi und Kunststoff GmbH
Lohweg 1
30559 Hannover
Tel. +49 511 – 53580
Fax +49 511 – 553394
info@jaeger-gk.de
Management:
Dipl.-Ing Sebastian Jäger
Julius Jäger, M.Sc.
Hanover Register Court HRB 59798
DE 813 314 161
Petra Dirlenbach