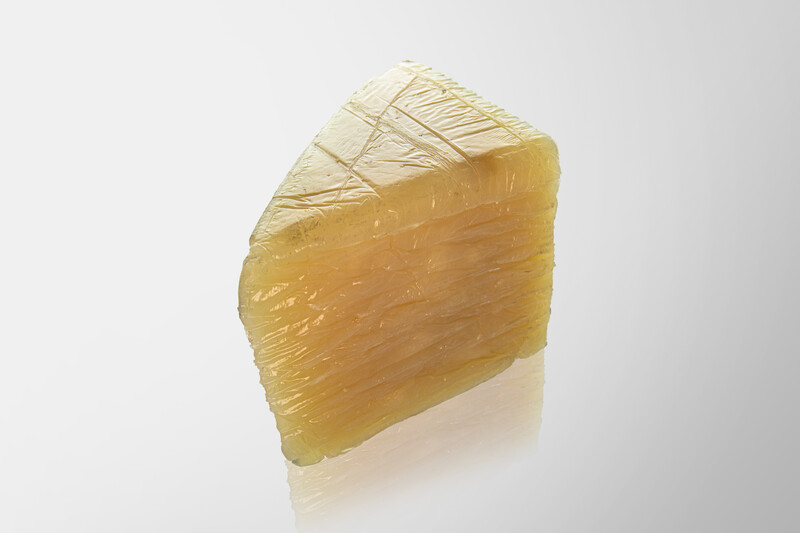
JÄGER Business Blog
making the rubber supply chain sustainable
WHITEPAPER
Find out which factors influence your SOP!
More and more processing companies in Germany have set themselves the goal of operating in a CO2-neutral manner – partly for intrinsic reasons, partly in response to the increasing pressure for action from society and politics.
However, it is important to bear in mind that sustainability does not just concern a company’s own processes, but includes the entire value chain, from the extraction of raw materials to the design and manufacture of products and their disposal. Companies that want to reduce their carbon footprint should therefore also put their supply chain management to the test.
On the organization side, there are some fundamental steps to clarify that have a significant impact on the carbon footprint in the rubber supply chain.
This concerns, for example, the make-or-buy decision. On the one hand, when rubber components are produced in-house, CO2 emission processes can be better controlled, analyzed and substituted. On the other hand, some manufacturing processes require specific know-how, which external service providers can contribute more easily. Their technical specialization enables improved capacity planning and thus lower CO2 emissions. Building up this knowledge in in-house production consumes considerable resources and is not always economical. In addition, specialized providers benefit from economies of scale that bring their greenhouse gas emissions per unit well below those of an in-house producer.
Internal logistics offer further potential for optimization. Inefficient packaging solutions create waste, the production and disposal of which generate unnecessary CO2 emissions. This is the case, for example, with rubber articles whose packaging units do not correspond to cardboard boxes or standard sizes. These have to be additionally packaged, secured or repackaged, resulting in more packaging waste. Switching to recyclable packaging materials or recyclable transport boxes is also a lever for improving the carbon footprint.
In addition, companies should take a close look at their ordering processes. There is often an opportunity to significantly reduce CO2 emissions by changing procurement behavior. Just-in-time structures, for example, are characterized by frequent deliveries that precisely cover the material requirements of a relatively short period of time. Replacing this approach, at least in part, with collective orders or framework agreements with larger delivery quantities has a positive effect on the CO2 balance and protects the environment.
The basis of a sustainable supply chain is a responsible selection of suppliers. First and foremost, companies should ensure that their suppliers comply with all legal requirements and have industry-standard certifications, such as ISO 14001 for environmental management and ISO 50001 for energy management. These simplify both supplier evaluation and proof to authorities. The second point is particularly relevant in Germany with regard to the upcoming Supply Chain Compliance Act.
In terms of location, local suppliers have a more favorable impact on the company’s carbon footprint than their competitors from the Far East. Although the global supply chain for natural rubber is spread all over the world (rubber trees grow mainly in Southeast Asia), short distances between customer and supplier offer some advantages. Article and material samples, partial quantities or returns, for example, are much easier to manage and more climate-friendly, as they cause lower CO2 emissions.
The same applies to communication. Even in the age of online meetings, face-to-face meetings are often unavoidable – and a train ride is less harmful to the environment than an intercontinental flight. In addition, it is important to remember that the EU has developed stricter climate protection requirements by international standards, which local suppliers must adhere to.
The complete rubber supply chain is difficult for companies to keep track of. From the extraction of raw materials to the finished part, on average four to five players are involved, many of whom are based in Southeast Asia. Contact is usually only with direct suppliers, so close collaboration is imperative to influence upstream suppliers as well.
Customers can assess suppliers’ sustainability efforts through environmental audits, such as ISO 14001, and companies should ensure that their entire supplier network is certified accordingly. If there are doubts about the legitimacy of the certification, for example because the auditor is close to the supplier, they can request a review by their own quality assurance department. However, this is a rare occurrence.
Document review
Companies should also ensure that their suppliers cover their own energy requirements from renewable sources as far as possible, gear their processes toward climate-neutral action and train their team accordingly.
If this is not sufficiently the case, the customer can support the supplier in optimizing its carbon footprint. This is easier to do with long-term partners, as the customer has a greater influence on the business relationship here. But new suppliers are often open to suggestions as well.
Parts of supplier management can be done digitally. In some situations, however, personal contact is necessary, for example when the customer visits plants as part of an environmental audit. Such business trips also cause CO2 emissions. While these are not comparable to production or transportation, they should still be considered. If an exchange of information can take place digitally, it should.
The carbon footprint of products depends not only on production and transport. Their entire service life is crucial. This also includes disposal.
At this point, reducing greenhouse gases in the rubber sector is somewhat difficult, because rubber products are difficult to recycle. To be sure, there are individual lighthouse projects that recycle rubber for specific applications. In practice, however, landfilling or incineration in waste-to-energy plants predominate, but these are not exactly beneficial to the CO2 footprint.
For this reason, the focus in the rubber sector is on waste prevention, not recycling. Starting points here are in design as well as in manufacturing on the supplier side.
A sustainable supply chain for natural rubber requires close cooperation between all the players involved, from raw material extraction to product manufacture. Individual companies have only limited influence on the overall process here. As a rule, all parties involved interact only with their immediate suppliers and customers.
It is therefore important to use the remaining levers as efficiently as possible. Companies should cooperate closely with their suppliers, minimize their own CO2 emissions, and pay attention to climate-friendly factors as early as the supplier selection stage. Every player in the supply chain must do their part to reduce environmentally harmful emissions, because this is the only way to establish a sustainable supply chain in the long term and mitigate the consequences of climate change.
Whitepaper: Secure the Start of Production
Learn which factors influence your SOP!
Torsten Schönwald is in charge of the rubber molded parts division in commodity purchasing at Jäger. The state-certified business economist has been with the company since 2018 and has been involved with logistics and procurement processes for more than eight years.
Share post now!
Jäger Gummi und Kunststoff GmbH
Lohweg 1
30559 Hannover
Tel. +49 511 – 53580
Fax +49 511 – 553394
info@jaeger-gk.de
Management:
Dipl.-Ing Sebastian Jäger
Julius Jäger, M.Sc.
Hanover Register Court HRB 59798
DE 813 314 161
Petra Dirlenbach