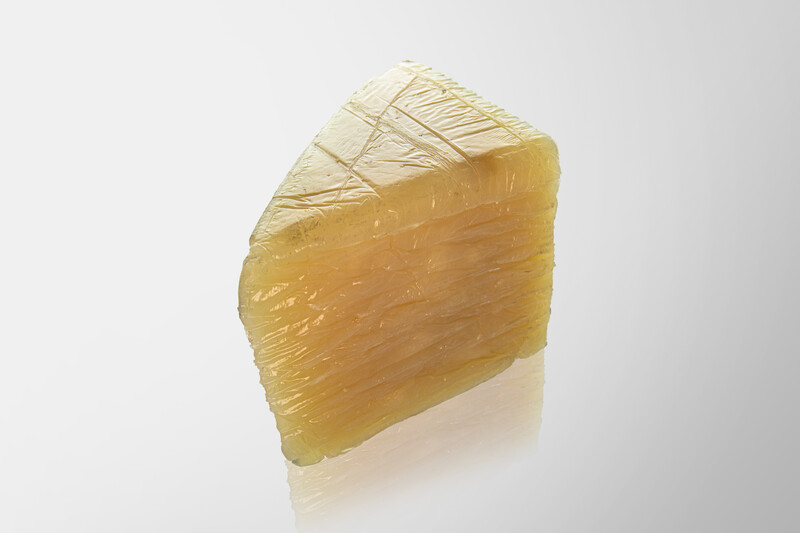
Technical article
what you need to know
WHITEPAPER
Find out which factors influence your SOP!
Supply chain management aims to plan, control and optimize material and information flows within a value chain. In the case of rubber and plastic components, there are numerous points to be set in this context, from the selection of suitable raw materials, material mixtures, suppliers and manufacturing processes to the intelligent timing of logistics and production processes.
In this article, we have summarized for you the most important aspects that you should consider in supply chain management with regard to rubber and plastic products. The information will help you to avoid typical problems. At the same time, you will find many tips that you can use to mitigate the negative effects of local and global crises – for example, shortages of raw materials as well as supply bottlenecks. This makes it easier for you to ensure your supply security.
Global Sourcing
In times of globally organized value creation, it is more important than ever to have a reliable procurement network. This network must enable your company to respond quickly and flexibly to changing needs within the supply chain. When dealing with rubber and plastic components, this presents several challenges for which you need to find solutions:
Until a few years ago, most companies were largely price-driven in their procurement of rubber and plastic components. If several suppliers offered goods of comparable quality, experience showed that purchasing always opted for the cheaper supplier. Due to lower labor costs, sourcing from Asia has therefore become standard in many industries.
However, purely price-driven global procurement can lead to incalculable follow-up costs in times of crisis. In transportation, for example, there are numerous starting points for unforeseen events (catastrophes, congested ports, etc.) and geopolitical risk factors (border closures, sea blockades, punitive tariffs, etc.), which can significantly delay the delivery of goods. In addition, long transport distances make it difficult to achieve sustainability goals such as reducing CO2 emissions. The extent to which foreign suppliers are preferable to local suppliers must therefore be carefully weighed up.
Since summer 2021, most industrialized countries have been experiencing an economic upswing. The number of newly registered corona diseases has decreased, at least temporarily. To this end, previous pandemic experience has established processes that enable manufacturing companies to manage corona-related impairments more effectively.
Accordingly, demand for raw materials and supplies has risen sharply. As a result, some resources (such as chemical precursors and plastics) are currently almost unavailable. This situation is particularly affecting producers who have so far purchased rubber and plastic products from individual suppliers.
Due to the high demand for raw materials, many suppliers are currently unable to guarantee fixed delivery times. In addition, corona-related transport restrictions regularly cause delays that negatively impact the entire supply chain – and in the worst case, production planning. Although it is possible to order goods with longer lead times, this requires sufficient storage capacity, which in turn entails higher costs. In addition, short-term supply bottlenecks cannot be eliminated in this way.
In some cases, rubber and plastic components are not given high priority in the design process. In addition, many development teams lack know-how in dealing with both materials, so that experience from metal processing is transferred to material groups made of rubber or plastic. This regularly leads to problems in practice, as many of the manufacturing processes used in the rubber and plastics sector (e.g. injection molding, pressing, extrusion) are not common when dealing with metal. Design drawings therefore often have to be adapted subsequently (e.g. due to geometries that cannot be implemented), which in turn has an impact on supplier management planning.
Achieving a stable price in the procurement of rubber and plastic components has always been a challenge for purchasing. The pandemic has even exacerbated the situation: due to fluctuating demand, prices for raw materials and input materials vary considerably. Consequently, this also reduces the planning reliability of manufacturing companies.
The Corona pandemic ruthlessly exposed how fragile globally ramified supply chains are in times of crisis. The fact that global supply chains are susceptible to disruptions is nothing new. However, the consequences in the event of an emergency have become clear for the first time since the virus spread with such intensity.
Corona acts like an accelerant in supply chain management, exacerbating existing challenges. In the rubber and plastics sector, however, there are a number of measures you can take to ensure your supply security in the short and long term.
The monetary benefits companies expect from global sourcing can quickly be negated by delivery delays. In addition, long transport routes make it more difficult to achieve climate protection goals and improve your own global footprint. It therefore makes sense to rethink procurement strategies, especially in times of crisis.
In manufacturing companies, the focus is currently shifting back to European suppliers. There are several reasons for this:
Companies that rely on a just-in-time purchasing strategy keep their inventories continuously at a low level. However, precisely planned individual orders are particularly vulnerable to price increases and disruptions in times of crisis. If a delivery does not arrive on time, this quickly affects the company’s production and delivery capability – and thus the satisfaction of its customers.
One way to protect against supply bottlenecks and price explosions is to conclude framework contracts with strategically important suppliers. These provide a high degree of planning security, as you define together with your supplier which orders must be placed in the coming months and on which dates. This is particularly important for specific rubber and plastic compounds, because suppliers do not have these products in stock as standard. In addition, the negotiation and organizational effort (and thus the process costs) is significantly lower compared with individual orders, as you do not have to negotiate new conditions for each individual delivery.
At the same time, you benefit from financial advantages with framework agreements. On the one hand, they offer greater price stability, since the purchase price for the goods ordered is fixed with the supplier and is not subject to fluctuations (apart from contractually agreed exceptions). On the other hand, the purchase of large quantities of goods creates scaling effects that you can pass on to your customers. If your production can process the entire order in one piece, for example, the setup costs of the machines and equipment involved and the costs for project management are reduced.
For rubber and plastic products, the most effective solution is often a compromise. Some suppliers have a dense network of sub-suppliers themselves and can outsource tasks as needed. The coordination effort required by a large number of suppliers can accordingly be outsourced to such production partners. At the same time, there may be financial advantages, as the supplier may be able to achieve economies of scale with its sub-suppliers. In other words, you benefit from the advantages of supplier consolidation without suffering the full extent of its disadvantages.
Test laboratory of the JÄGER Group
Rubber and plastic components are often neglected in design. At the same time, development teams usually lack the necessary experience in dealing with these materials. As a result, manufacturing companies often confront their suppliers with design specifications that cannot be produced in the intended form. In addition, the lack of expertise means that potential for improvement, which could be exploited by the design department with the appropriate know-how in terms of material selection and design, remains unused.
To avoid additional development loops and to design rubber or plastic components ready for production on the planned date, you should work with a specialized development partner as early as possible. Ideally, you should integrate their experts into your team in the early phases of the project. The earlier you provide your supplier with all the relevant information about your development project in the form of a specification sheet and discuss it with material specialists, the more efficient the development process will be.
The Corona crisis showed how important close cooperation between customer and supplier can be in an emergency. Companies that integrated their suppliers into their own process chain in a meaningful way were able to respond more quickly to delays and outages, for example. In many cases, this at least mitigated the effects of the pandemic.
You lay the foundation for integrating your suppliers at the IT level. Instead of forwarding orders and information to your suppliers via e-mail, you should network them with your IT landscape. This makes it possible to exchange all necessary information (orders, delivery bills, invoices, requests, etc.) digitally.
There are numerous advantages to be gained from such a connection: With the help of an EDI connection, you can, for example, create a dynamic preview of your goods requirements for the coming months so that your supplier can prepare production orders and deliveries in good time. Alternatively, you can network your ERP system with that of the supplier. This makes it possible, among other things, to automatically trigger purchase orders based on your goods requirements (or your inventory). Functionally, this solution corresponds to an EDI connection, but there are no costs for setting up an EDI server.
It is also worthwhile in logistics if you integrate suppliers into your processes. This reduces friction losses and ensures that materials and components arrive at the right place at the right time. One example of this is order picking. If your supplier delivers the ordered rubber or plastic component in packaging units that correspond to your planned consumption, your warehouse staff will save a lot of effort because they will need less time to decant and sort the delivery. The boxes can be taken directly from the pallet and processed further. At the same time, you save a not inconsiderable amount of packaging waste.
In supply chain management, high responsiveness and flexibility are key success factors. These are easier to achieve if you focus on long-term cooperation with your suppliers, which is characterized by openness and trust.
On the basis of such a foundation, agreements between customer and supplier are faster and less complicated. Problems can be resolved more easily if both sides know each other personally. In the event of delivery delays, for example, it is more practical to contact a long-standing business partner by phone instead of contacting customer service by e-mail. In addition, cross-company collaboration runs more smoothly with long-standing partners. Conflicts that are the result of differing goals and expectations arise much less frequently in such cases. In addition, both sides can anticipate problems in many cases because they know how contact persons will react in certain situations.
Last but not least, long-term collaboration with suppliers brings you financial benefits. On the one hand, there are no process costs for research, contract negotiations, and supplier qualification, which take a certain amount of time to pay off in the case of new partners. On the other hand, suppliers often offer lower prices for long-term existing customers. After all, they have an interest in the continuation of the partnership.
Overview of a calculation curve
In the rubber and plastics sector in particular, you should constantly monitor developments on the raw materials market. Supply problems with certain resources and materials are usually the result of developments that experts can predict quite precisely. If you recognize these developments, it will be easier for you to take countermeasures in good time.
If you lack the resources or expertise to monitor the raw material markets, it is worthwhile to exchange information with rubber and plastics suppliers. They have been dealing with developments on the market for years and, if necessary, can quickly provide information on which alternative raw materials with comparable properties are currently available. At the same time, you can obtain forecasts from suppliers about expected price developments and restrictions, e.g. if certain materials are banned due to political decisions.
Especially in times of crisis, it is advantageous not to be dependent on the availability of certain raw materials. Your company can achieve this flexibility by ordering alternative material blends with comparable properties for its rubber and plastic components. This does lead to higher costs, as these compounds have to be designed and tested. In return, you can fall back on alternative raw materials in an emergency and ensure your supply security even if resources are temporarily unavailable.
The search for alternative materials is worthwhile not only for new developments, but also for existing products. This is not just about your supply security. Since materials management is constantly evolving, older products often reveal potential for improvement, which you can use to optimize your carbon footprint, among other things. There are also often opportunities to change the design of the component and reduce weight or increase functionality by adapting the material. Material costs and the service life of the molded part can sometimes be significantly improved by such changes.
Substituting raw materials and developing alternative materials is not possible in the short term in every industry. For example, materials in the food or medical technology industries have to go through complex approval processes before they are released for production. If this is also the case in your company, you need to plan sufficiently ahead. However, with a view to future crises, this procedure may also be worthwhile in your case.
Production of a tool
In injection molding manufacturing projects – whether for rubber or plastic components – mold making is one of the most complex, time-consuming tasks. Injection molds are precision tools that must be individually manufactured, tested and approved for each new order. Numerous sources of error lurk here, which can delay projects and impair downstream processes in the supply chain.
You can neither shorten nor accelerate the construction of a new tool. Accordingly, you must allow sufficient time for this in the project planning. It is a good idea to integrate a rubber or plastics manufacturer into the project as early as possible in the development phase, as they have material expertise and can contribute positive impetus to your development project on the basis of their experience. Experience has shown that you can meet deadlines more reliably in this way. In addition, you can identify and eliminate sources of error at an early stage.
If you have your tool manufactured by an external partner, you must keep an eye on the associated logistics. Here, too, a price-driven approach is currently not always the best decision. In the case of international toolmakers, for example, delays can quickly occur during transport, whether due to crises or bad weather. In addition, corrections are complex, as the faulty mold design may have to be transported over thousands of kilometers.
Storage racks in the logistics center
Rubber and plastic components bring with them specific requirements for transport and storage. If handled improperly, the sometimes highly sensitive components can be damaged and thus become unusable. This is another reason why supply chains in the rubber and plastic sector are more susceptible to disruptions than is the case with other components.
In the case of plastics, for example, natural conditioning can occur depending on the material. The plastic absorbs water at higher temperatures or humidity, and the item’s properties change so that it can no longer be installed. Rubber compounds, on the other hand, have a limited shelf life and must be processed as quickly as possible. The compound material begins to age after about four weeks and loses some of its properties. You should also note that pre-vulcanization can occur if you do not comply with the temperature specifications during transport.
To prevent these problems, you should strictly adhere to the compound-specific specifications of the manufacturer (storage temperatures, transport conditions, etc.). So a close exchange with your supplier is also recommended with regard to transport and storage. This makes it easier to coordinate the processes in your supply chain. In addition, it also makes sense in terms of logistics to maintain redundancies in the supply chain. If you have approved several rubber compounds, you can react more flexibly to disruptions.
To prevent crisis-related problems, it may also make sense to re-evaluate your inventory strategy. If you increase your safety stock levels, your production can temporarily compensate for delivery shortfalls, for example. It may also make sense to adjust your lot sizes. Instead of ordering material quantities as needed at short intervals, you can place larger orders and keep some of the material in stock.
In light of the current shortage of raw materials, more and more manufacturing companies are turning to bartering with competitors. For this purpose, there are digital trading platforms where companies can offer or search for resources. If your supplier cannot currently supply a particular raw material and there is no alternative resource or blend available, it makes sense to consider this option.
Network of diverse suppliers
Supply chain management is a complex process in which numerous companies within a supply chain cooperate and depend on each other. Accordingly, a robust sourcing strategy requires reliable information about all suppliers and sub-suppliers. For example, you should know how your partners’ procurement and supply processes are structured. In view of sustainability requirements, you also need information on where your suppliers obtain resources. As an informational basis, it is advisable to have a detailed supplier database that you update regularly. Among other things, this will create the ideal conditions for risk analyses in which you review your entire supply chain.
The prerequisite for stable supply chain management is a network of reliable suppliers. Particularly in the procurement of rubber and plastic materials and precursors, supplier selection is therefore of high strategic importance.
In the current situation, a price-driven approach to the selection process is risky. Instead, the focus of your search should be on how you can make your supply chain more crisis-proof. To do this, you need to sound out the market for rubber and plastics suppliers in detail, taking into account not only costs but also aspects such as reliability and quality.
To ensure that your supplier meets all relevant requirements, you should evaluate all candidates according to meaningful criteria. In addition to economic aspects, ecological and social factors also play a role – keyword sustainability. Corporate social responsibility goals, for example, are easiest to meet with reliable, transparent processes and short supply chain distances. Orientation is provided by international management standards such as ISO 14001, which defines the essential requirements for corporate environmental management.
Jäger Gummi und Kunststoff's offerings are based on a robust network of sub-suppliers, approximately 96 percent of which are headquartered within the European Union (80 percent in Germany). Sustainability plays a dominant role in this network. Thus, suppliers are selected based on their certification to the environmental standard DIN EN ISO 14001 as well as (ideally) DIN EN 50001.
Facing problems proactively and reacting flexibly to disruptions is becoming increasingly important in supply chain management. These capabilities require a range of measures in rubber and plastic products, from the careful selection of reliable suppliers to the close integration of all supply chain partners into your processes and systems.
You will achieve the best results by implementing as many of the measures presented here as possible. In some areas, this may increase the effort required for your supplier management. However, the result is a robust, reliable supply network that you can maintain even in the event of crises occurring at short notice.
Whitepaper: Secure the Start of Production
Learn which factors influence your SOP!
Share this post!
Jäger Gummi und Kunststoff GmbH
Lohweg 1
30559 Hannover
Tel. +49 511 – 53580
Fax +49 511 – 553394
info@jaeger-gk.de
Management:
Dipl.-Ing Sebastian Jäger
Julius Jäger, M.Sc.
Hanover Register Court HRB 59798
DE 813 314 161
Petra Dirlenbach